Parcel Distribution
Fives offers turnkey solutions to automate our clients’ entire parcel handling process.
With a wide range of intelligent state-of-the-art technologies at our disposal, we design parcel distribution solutions that meet customer requirements perfectly in terms of performance, accuracy and reliability.
Our solutions handle every type of parcel and can be adapted to deal with changes in volumes and operations.
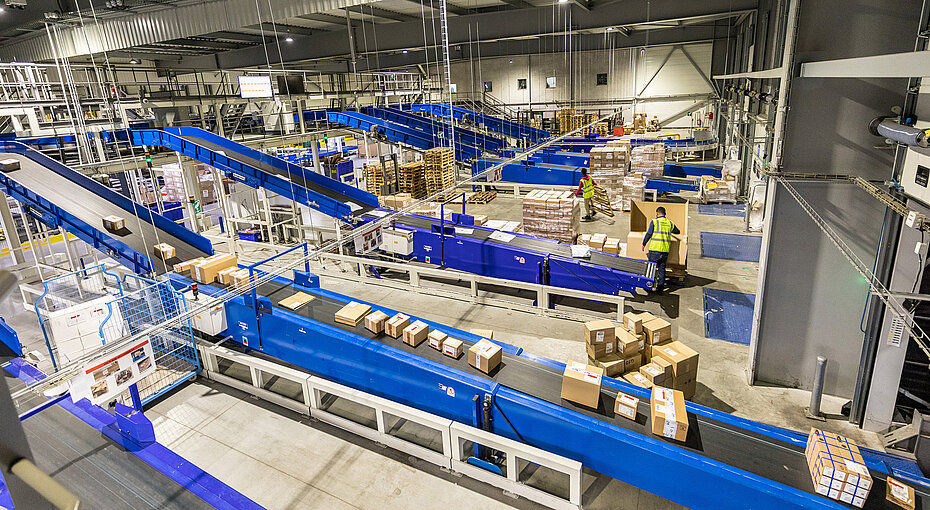
Parcel offload
Incoming parcels can be offloaded from trucks by telescopic boom conveyors extended directly into the trailer or by conveyors at vehicle unloading docks. When parcels are transported in cages, containers or pallets, workers offload them with forklifts or other vehicle unloaders.
The contents of the pallets, cages and containers are unloaded onto upstream conveyors by automated tippers. The upstream conveyors connect the offloading zone with the singulation and sortation area.
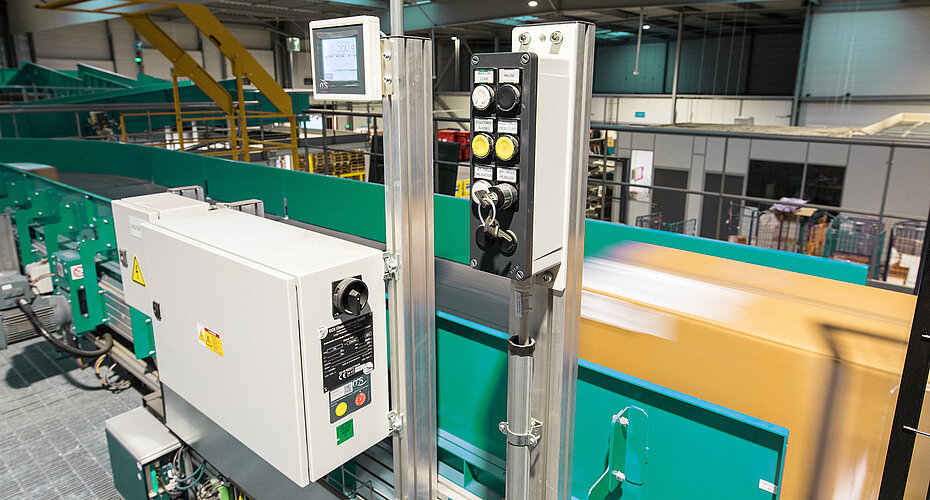
Check weight and cube (CWC)
Items entering the distribution center go through check weight and cube (CWC) devices that measure the dimensions and weight of each parcel.
Parcels are conveyed under reading stations that scan their labels and collect all the information needed to sort them to the correct destination.
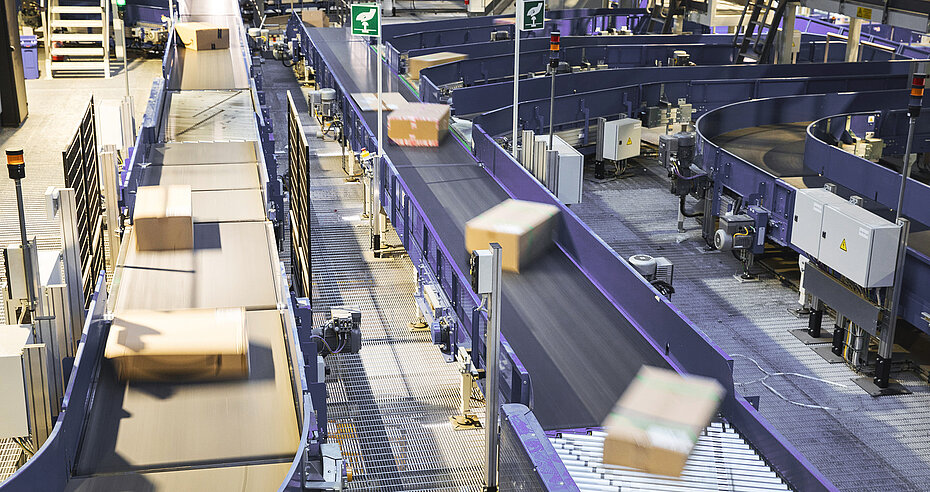
Conveying
To optimize the transportation of parcel flows within the distribution center, modular roller and belt conveyors are used as upstream lines. They transport incoming parcels from the offload area to sorter equipment, while downstream lines transfer outgoing parcels from the sorter to the outputs. Lines of conveyors are also used to connect, merge, split, bypass, buffer, recirculate and take away material flows.
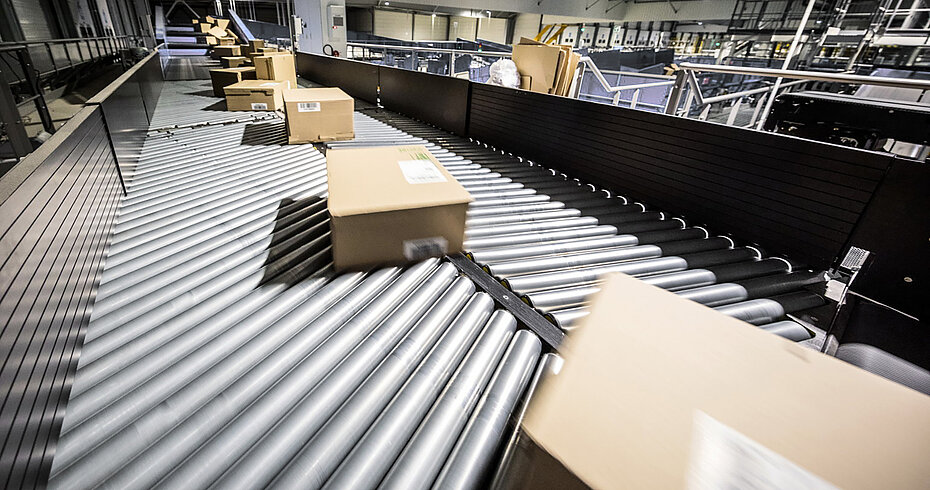
Singulation
If the material flow comes from automated tippers that tilt the contents of pallets and cages over the conveyors in bulk, singulation optimizes sorter feeding, improving accuracy and capacity. The singulator handles bulk flow automatically, converting it into a stream of singulated parcels. As they leave the singulator, parcels are properly aligned and spaced one by one, ready to be transferred to induction lines.
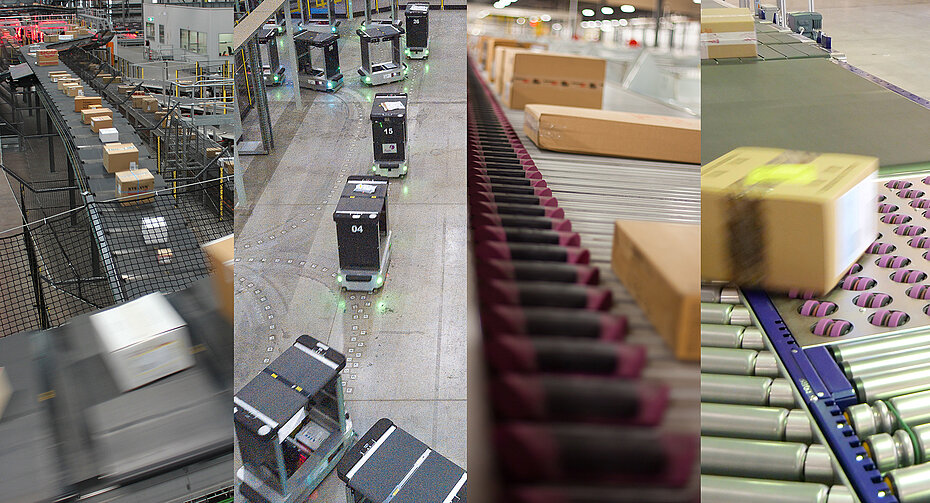
Sorting
After they go through upstream and singulation, incoming flows are sent to the sorter.
Each parcel that enters the sortation system goes through a reading station that scans the parcel barcode containing all the information needed to sort the parcel to its destination.
When a sorting solution based on loop cross-belt technology is used, parcels are transferred to a sorter cross belt via automated induction lines or manual loading positions.
The sorter transports parcels to the allocated outlet according to the sorting plan. The outlet can be a conveyor, chute, bag, roller cage, or any other container that receives all the parcels addressed to the same destination.
When the sorting solution includes a linear sortation system, the induction conveyor transfers the parcel flow from the upstream to the sorter in a line. The linear sorter sends each parcel to its assigned output using sliding shoes or diverters. The outputs consist of conveyor lines that transfer the parcels to the next stage.
Our innovative sorting solution makes use of autonomous mobile robots (AMRs) as mobile sorters equipped with standalone cross belts. Parcels can be loaded manually or automatically onto the cross belts. Then, each AMR moves through the sortation area to transport parcels to their outlets. An optimized route is calculated for each robot according to its position. Once the AMR reaches its destination, the cross belt discharges the parcels into the corresponding outlet.
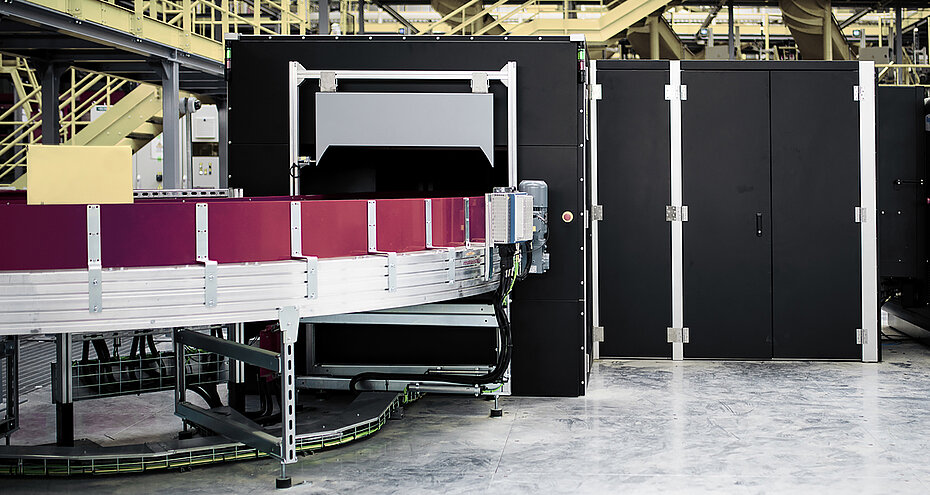
Security screening
Parcels that require security screening are diverted to a special area with automated or manual X-ray machines and explosive detection systems (EDS) connected to the transport system.
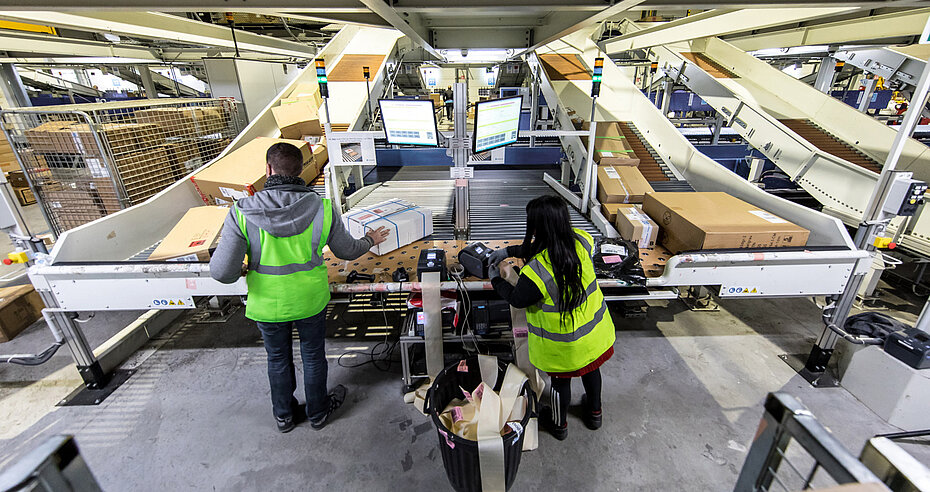
Manual reworking
Cases sometimes require manual reworking. This could happen, for example, due to a missing barcode label, a no-read, or a lack of assigned outlet. In these instances, a conveyor system transfers parcels to dedicated manual working stations. Operators re-work the parcels before loading them onto the conveyor for transfer to the next processing point.
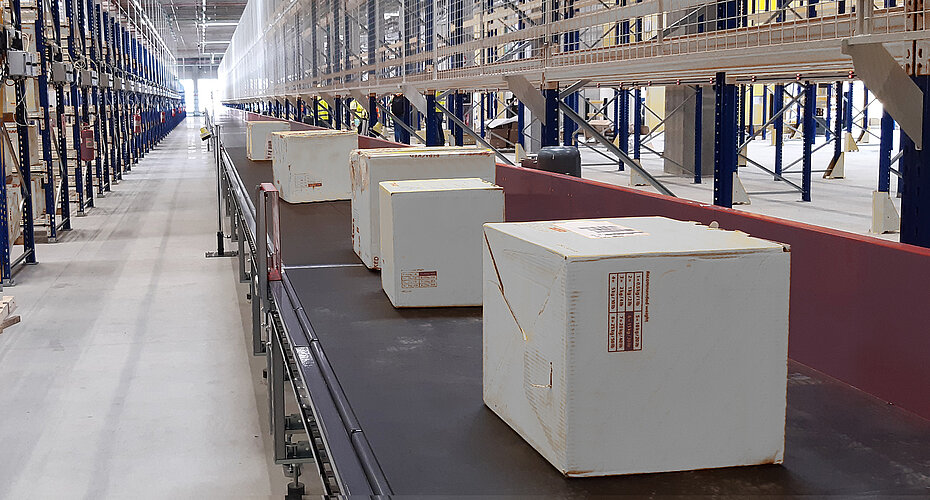
Customs clearance
Our processing systems integrate tailor-made solutions to facilitate customs clearance operations inside distribution centers.
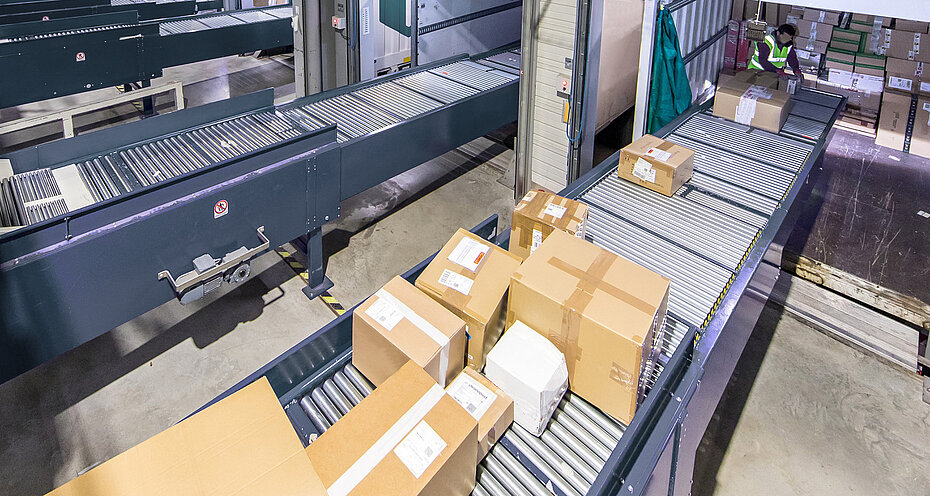
Reload
Sorter outlets are connected to a downstream conveyor system that transports sorted parcels to the reloading zone.
Parcels are then loaded from the conveyors into trucks at the outgoing docks for transportation to their final destination. Parcels can be loaded as loose loads or in pallets, cages and containers, both manually and automatically.