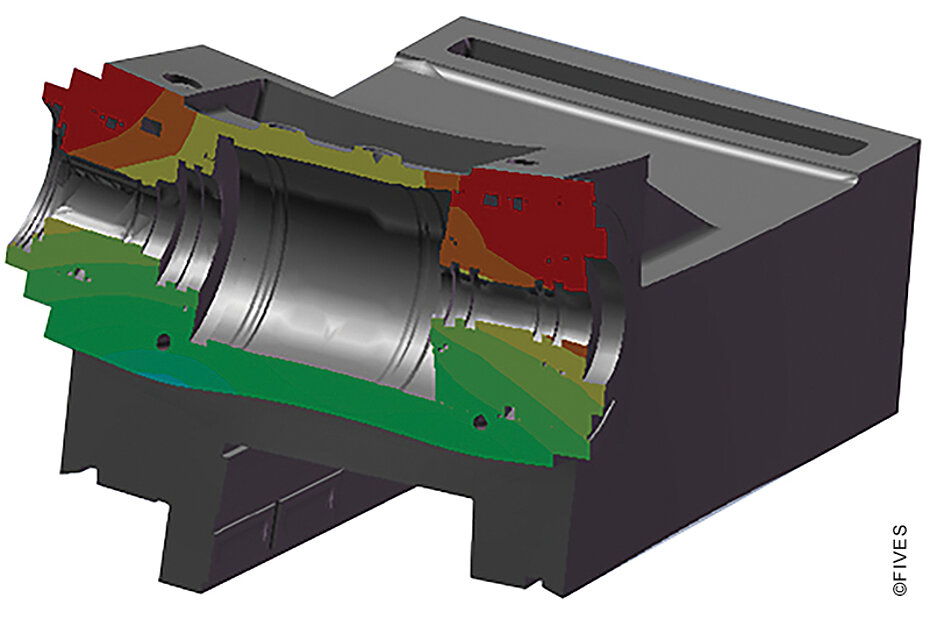
THE PROBLEM
When taking the next step toward greater production accuracy on a machine where stiffness, damping and abbe errors have been reduced to a minimum, it is often thermal effects that remain dominant and prevent the desired improvement in product specification. When using standard chiller systems for temperature control, the on/off control of the system can often be seen imprinted in the surface of precision optics. Some fluid chillers claim ±0.1 °C control, but in order to achieve sub-micron form error across the surface of an optic, it can be necessary to go further, with a target of ±0.01 °C.
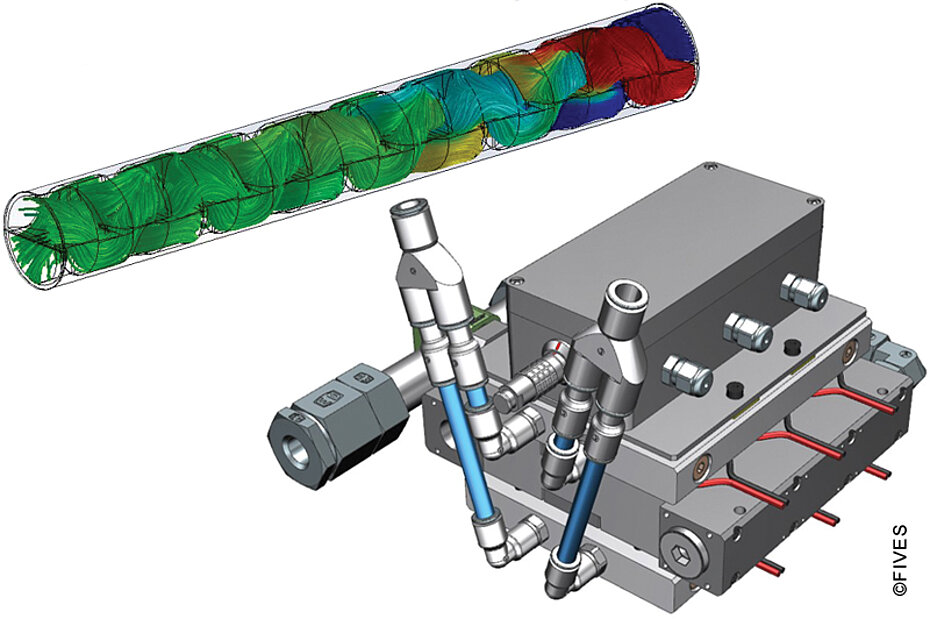
THE SOLUTION
A small thermal control unit was designed that could be retrofitted to existing fluid control circuits on the machine. Taking the standard temperature control capability of a normal chiller system, say ±0.1 °C, fluid temperature deviation is corrected further and smoothed to reduce hysteresis and overall fluctuations. CFD was used to ensure optimal fluid flows and thorough mixing of fluids to guarantee uniform temperatures of all circuits.
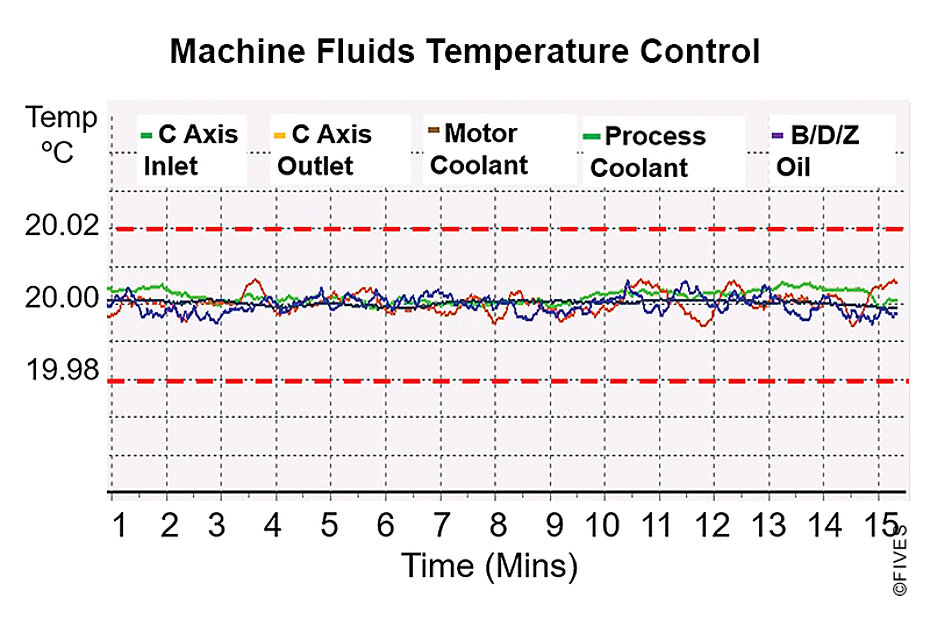
the result
- Multiple circuits controlled to better than ±0.01 °C, including motor cooling, hydrostatic oil and process cutting fluid
- Sub-micron form errors across ground component surfaces – no corrective form polishing required
- Scalable solution for larger machines and fluid volumes
Check out our Engineering Partnership brochure to learn more about our available offers.