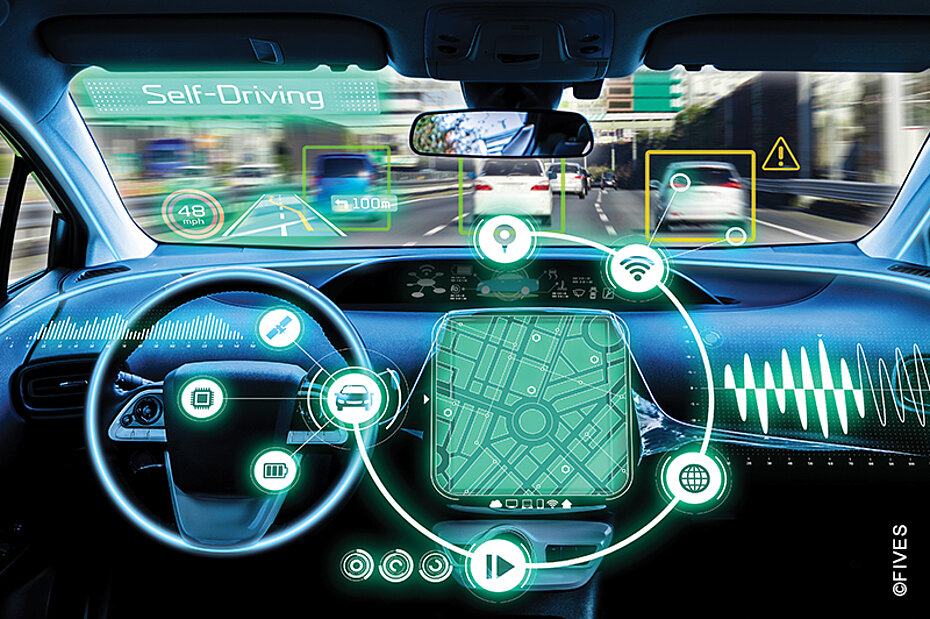
THE PROBLEM
Manufacture high precision optical molds used in vehicle head-up displays (HUD) and camera lenses, for automotive and mobile applications. Optical molds, which often require complex and freeform geometry, are made from materials that are difficult to grind (stavax and tungsten carbide), thus require many hours of post-grinding corrective polishing.
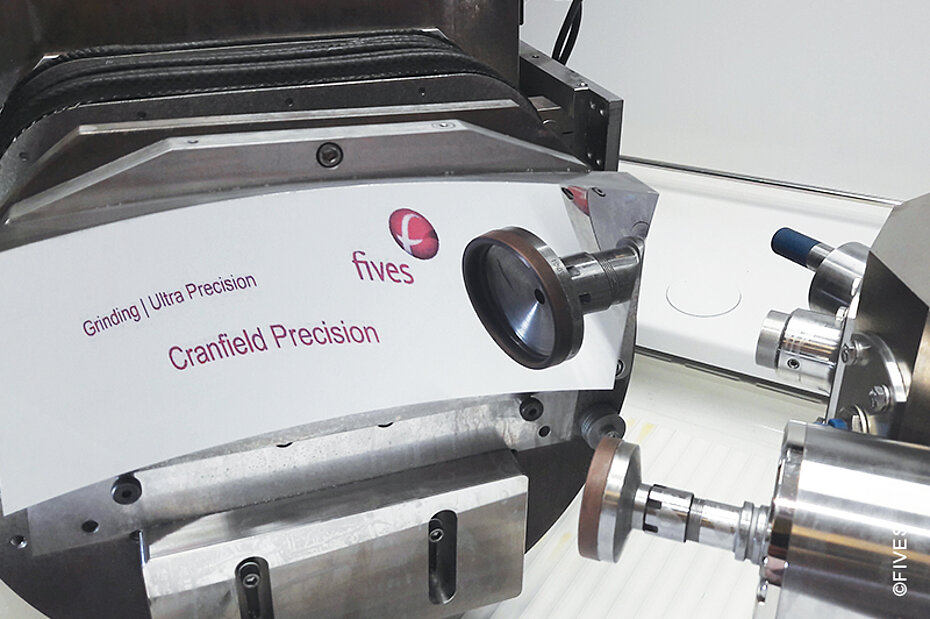
THE SOLUTION
Cranfield Precision engineers developed a solution that takes the optical molds surface design and generates the necessary grinding operations for the freeform and complex geometries. Tooling is carefully designed, selected and then tested in our ultra-precision machining lab. The complex and freeform optical molds are ground using unique grinding machinery that has class-leading stiffness, damping and thermal stability.
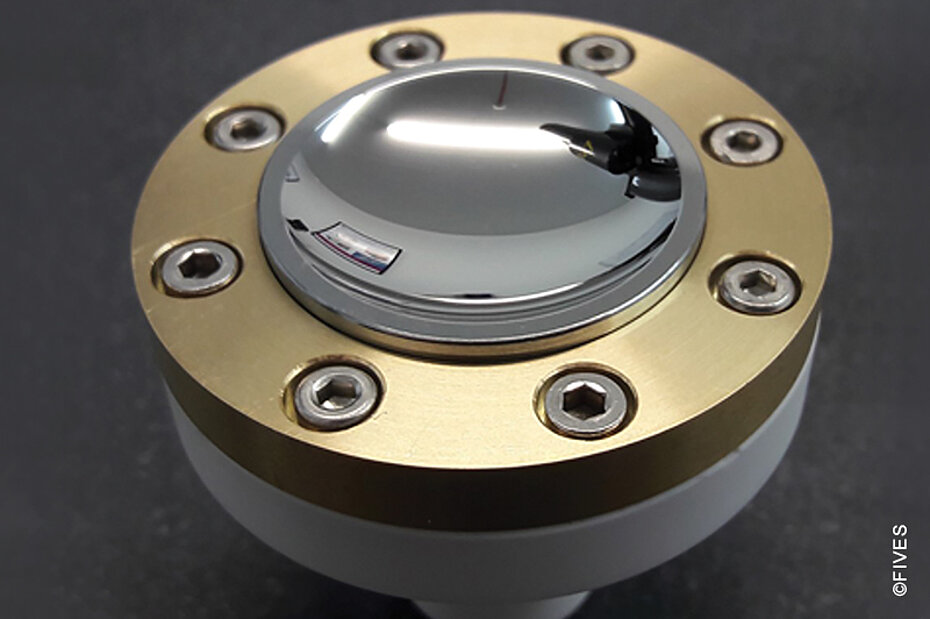
the result
- Low form error
- High quality surface finish; near polish quality
- Minimal SSD
- Minimal post-polishing required
Check out our Engineering Partnership brochure to learn more about our available offers.