Furnaces for a full range of heat treatment: from preheating before forging, to normalizing, annealing, stress relieving, tempering and hardening. The heat treatment furnaces give you temperature homogeneity, optimum combustion control thanks to the AdvanTek® burners, low fuel consumption, flexibility of operation and performance reliability.
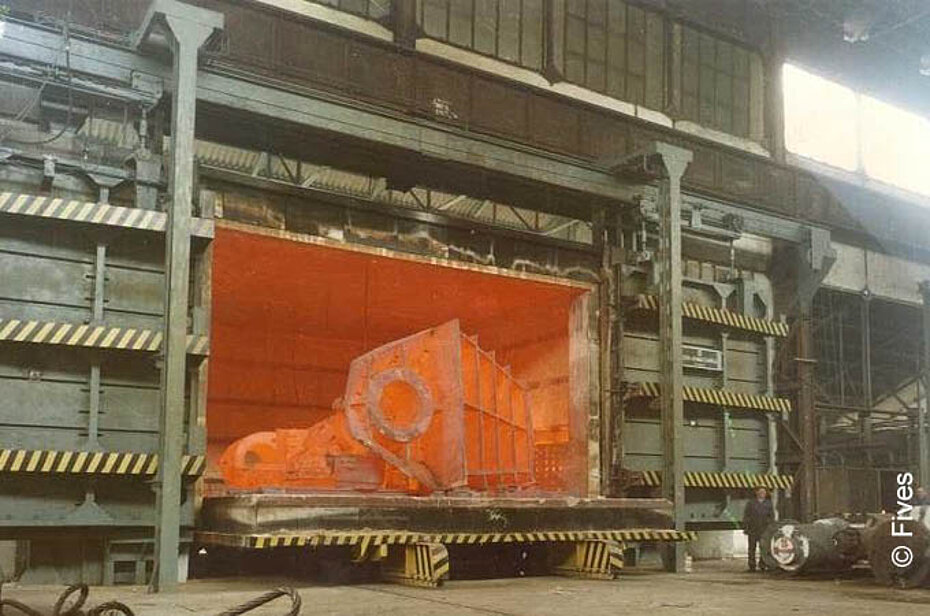
BOGIE HEARTH FURNACE
With heat treatment temperatures from 600 ̊C to 1,350 ̊C, this furnace is typically used for bars, plates, coils & tubes:
- Preheating before forging
- Stress relief in metal products, pressure vessels, rolls
- Various annealing processes
- Quench and tempering
- Normalizing
Electric heating is also available. This furnace is very flexible: the bogies are loaded outside the furnace and can either use a push or pull (truck & pulley) mechanism to enter the furnace. You can have more than one bogie in use at a time, so that one load is ready to go while the other is still in the furnace.
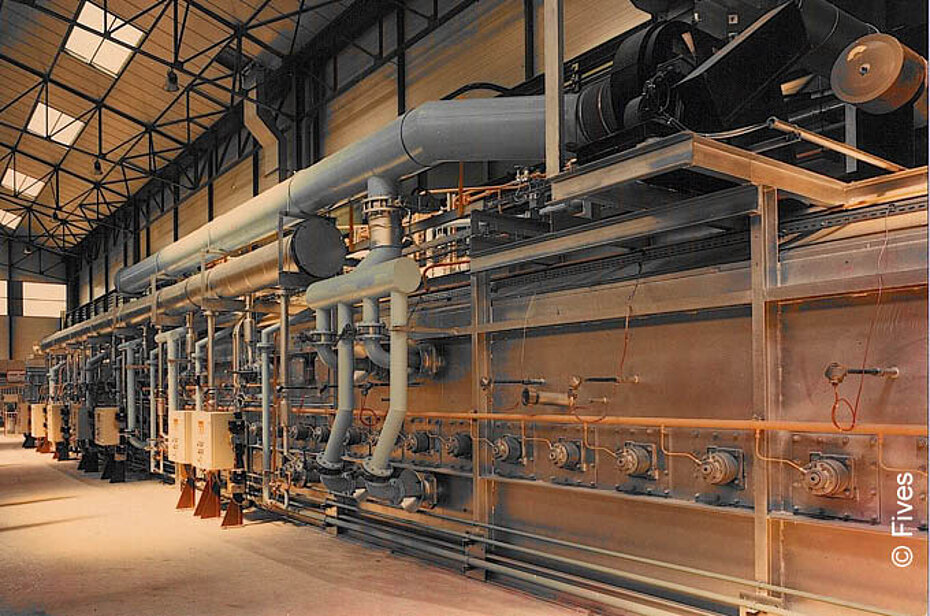
ROLLER HEARTH FURNACE
Used for bars, tubes, wire rod coils and heavy plates, with heat treatment temperatures from 600 ̊C to 1,050 ̊C, with or without protective atmosphere, for such applications as:
- Annealing
- Quench and tempering (austempering)
- Normalizing
- Stress relief
Electric heating is also available. Burners and rolls can be pre-mounted in sections to reduce the overall installation time. Installation is quick and easy thanks to the modular design, which includes different types of lining. All of the components are fully automated and controlled.
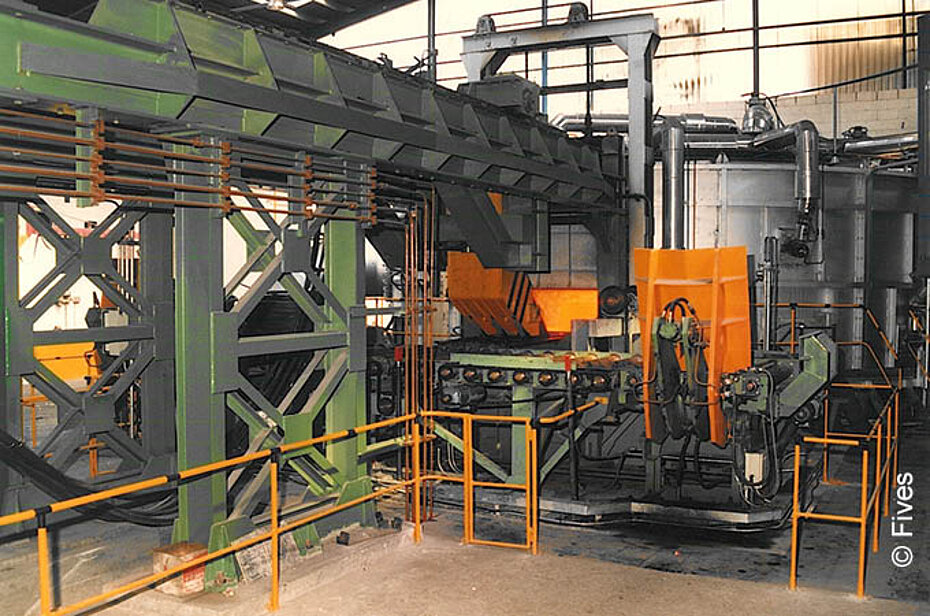
SPECIALTY FURNACES
They can be operated with a variety of fuels to achieve process temperatures up to 1,200 ̊C.
These furnaces are used to heat treat strip coils, wired rod coils, cast iron tubes or graphite electrodes. The range includes:
- Rotary hearth furnaces
- Bell furnaces
- Graphite electrode bogie hearth furnaces
- Chain pushers
- Chamber, in/out furnaces
- Vertical or horizontal ladle preheaters and dryers
- Controlled cooling hoods or cooling beds for tubes
Rotary hearth furnace
A rotary hearth furnace is designed for reheating any semi-finished products, such as round or square billets (carbon or stainless steel) for seamless pipe mills and forging plants, high grade steel ingots for railway wheels, as well as heat treatment (annealing, quenching) of wire rod coils. Modular design and customized charging and discharging machines ensure optimum performance, while the simple and robust design guarantees easy maintenance.
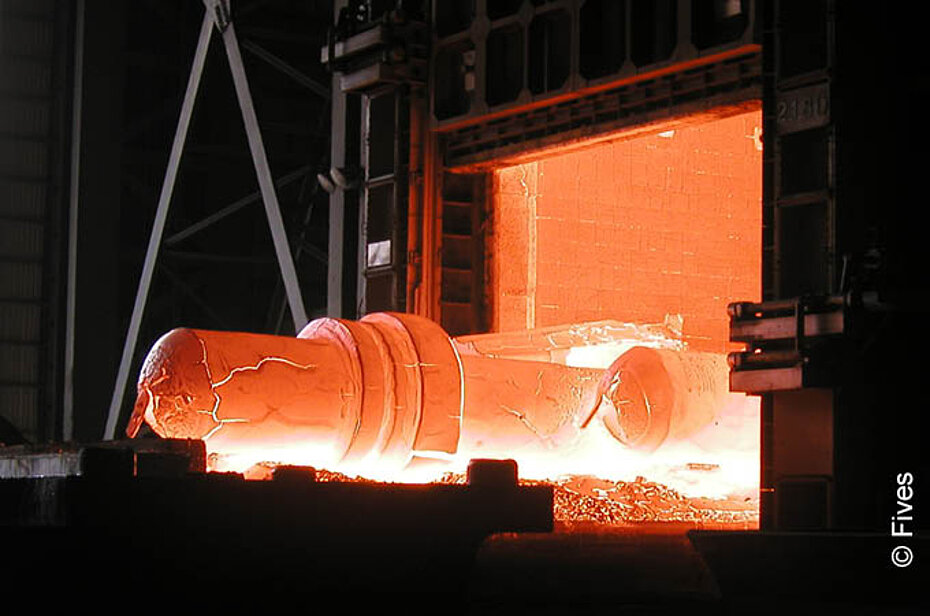
FORGING FURNACE
Used for the heat treatment of ingots, square or round billets, those are in operation in wheel forge shops:
- Continuous rotary hearth furnaces with charging & discharging machines
- Batch type bell or chamber, in/out furnaces
- Pit furnaces
- Bogie hearth furnaces
In these furnaces, the products can be loaded either in vertical or horizontal arrangement depending on their dimensions. Fully automated charging and discharging machines can be supplied upon request.
Mobile transport manipulators and special tongs with 90º orientation during loading and unloading from the furnace can also be used.