Graphitization is a process for heating graphite to very high temperatures in a controlled environment, in order to improve its physical structure. It is used in the aerospace, aeronautics and automotive industries for the manufacture of brakes, clutch facings, mechanical seals or composite materials.
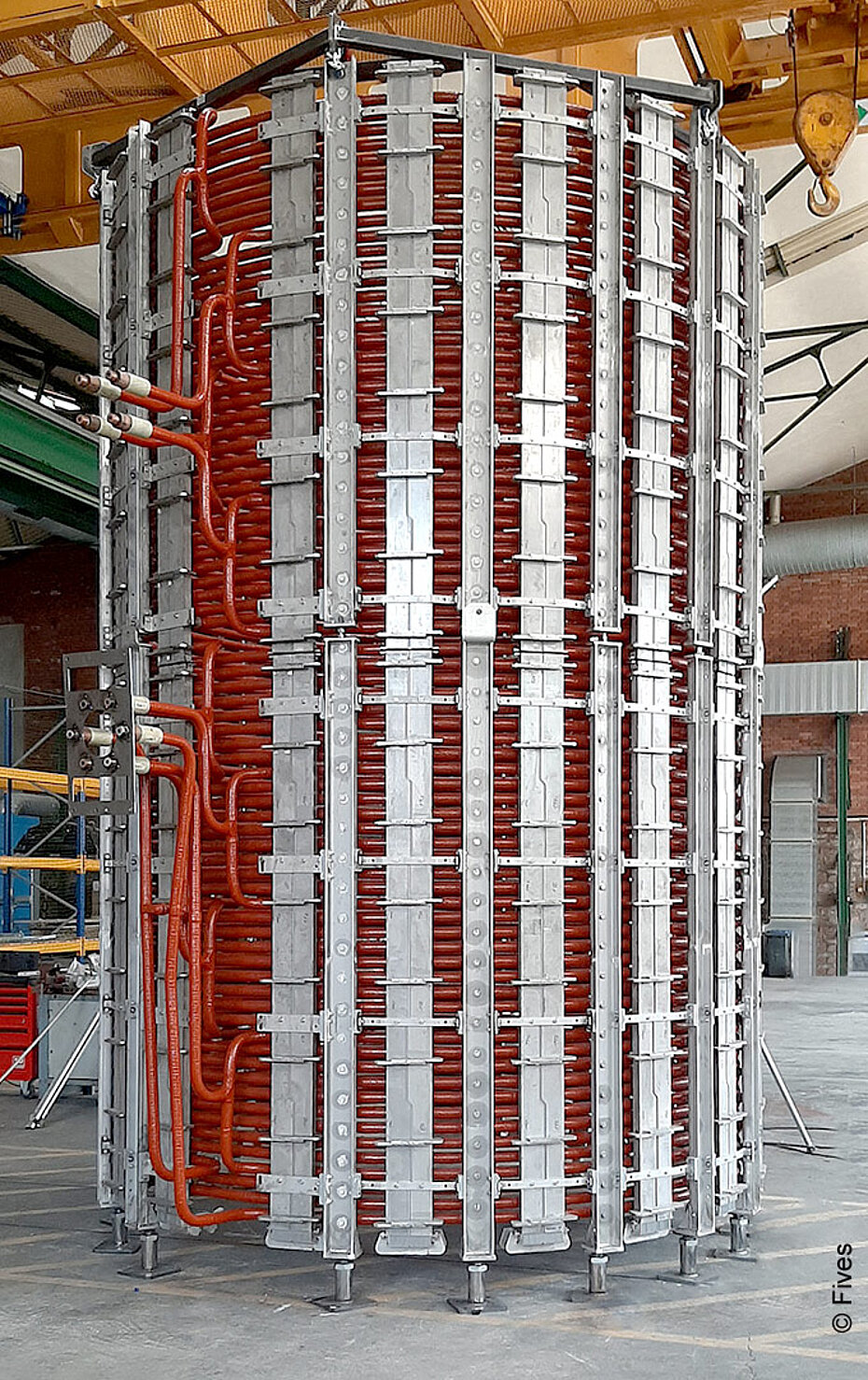
Advanced process
Our induction graphitizing furnaces heat carbon parts (porous or not) to a temperature of between 1,000 and 2,800°C and impregnate them with a moist gas.
A graphite susceptor is heated by induction. The energy is then transmitted to the treated parts by radiation. The inductor and the susceptor are placed in a chamber where the required pressure cycle takes place. The starting power of the most modern systems exceeds 1,000 kW.
The parts can undergo long treatments and pressure matrix cycles in a reducing atmosphere.
Smart solution
Our induction graphite furnace solutions are ideal for complex heat treatments and unbalanced furnace loading.
The advantages of our solution are as follows:
- Rapid and controlled temperature increase
- Continuous temperature modulation in each zone
- Continuous leakage protection (maximum safety)
- Power factor > 0.92 over the entire power range
The CELES IS power converter offers the possibility to distribute and modulate the power injected on the susceptor in several distinct zones. This enables you to maintain the homogeneity of the temperature inside the chamber for the highest possible quality.