Assistance
Assistance from Expert Engineers
For maximum performance and minimal downtime, you need a partner you can trust. Our expert engineers are available by phone, email, and at your plant to assist with queries, troubleshooting and performance optimization
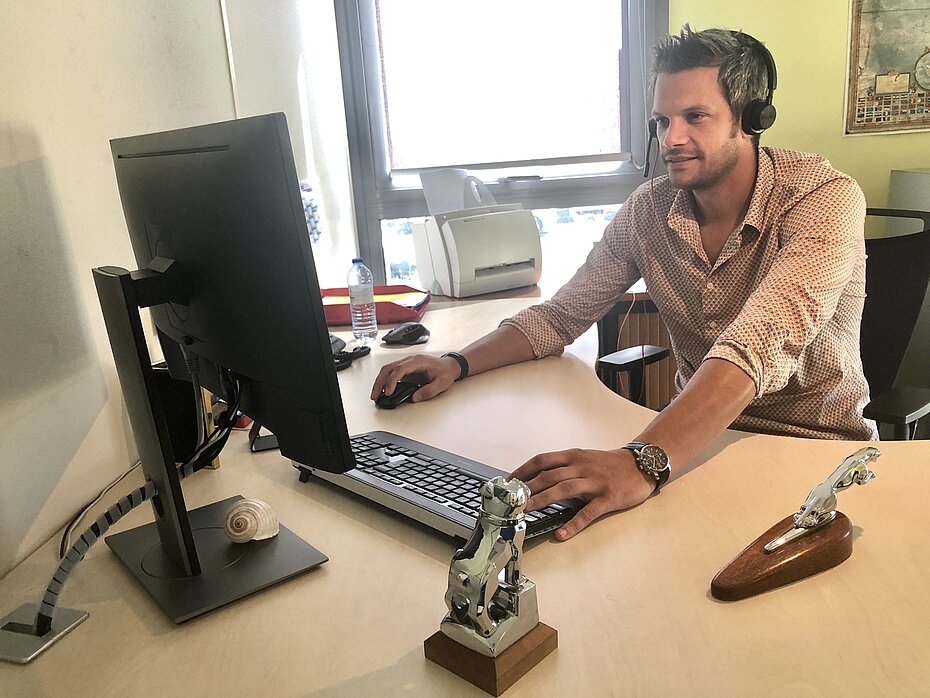
Expert engineers at the end of the phone
If you have a question or need help with your filling, sealing or testing equipment, call our experts.
Our hotline is staffed by process experts and commissioning engineers with direct operational experience of all our machines. Open during office hours Monday – Friday, the Hotline is your first port of call for all enquiries.
+33 2 40 32 06 06
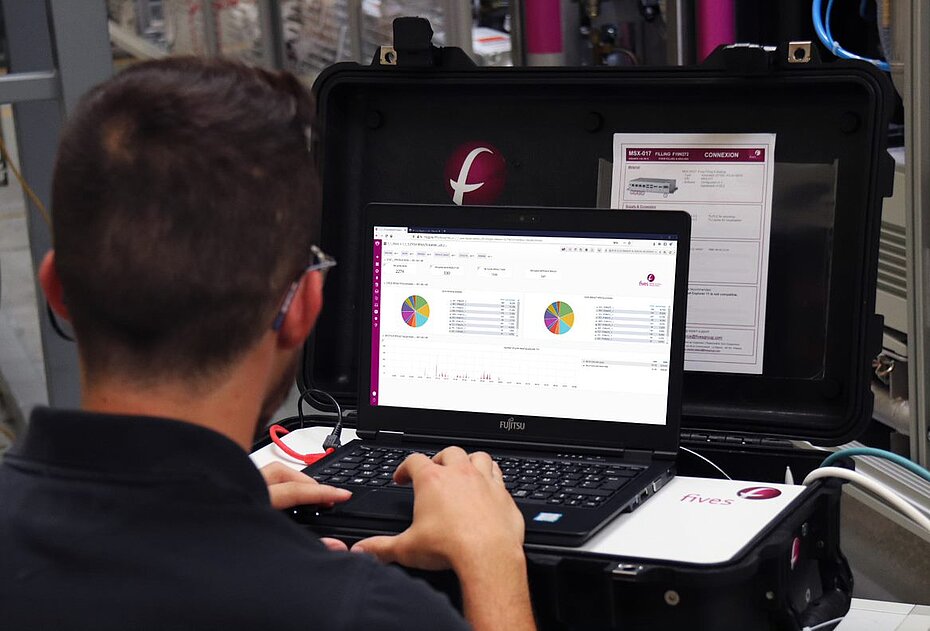
Troubleshooting services
With uptime and reliability the highest priority, you can put your faith in our expert engineers.
If we can’t help you resolve your issues over the phone, we’ll send an engineer to your site. We’ll conduct a full root cause analysis to identify the source of the problem, fix it, and prevent it recurring.
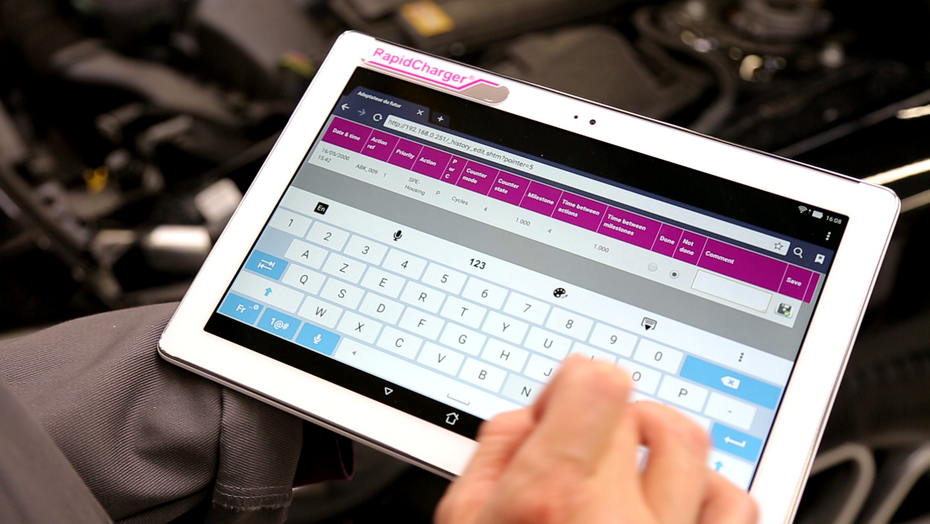
Remote capabilities
Sometimes, as we are all too aware, travel is restricted and visits to site are not an option.
We are developing a range of remote services, including a smartphone app, that make remote troubleshooting a viable alternative. The app includes advanced augmented reality technology to help our engineers diagnose process problems.
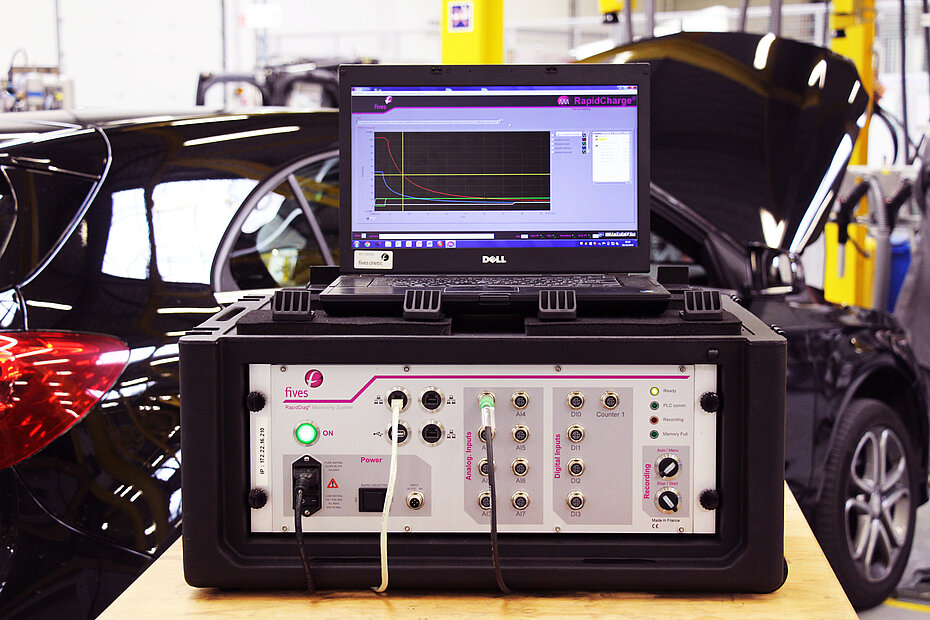
Performance optimization, monitoring and audits
If you find your equipment is not performing as expected, we can help. Our performance optimization services include equipment monitoring and auditing.
Our expert engineers can help identify where things are going wrong and how to put them right. And if you need to optimize cycle time and get more from your equipment, we can make that happen.
One of the ways we can help is with our digital data tool, the RapidDiag®. The RapidDiag® Complete Data Acquisition System collects real-time performance data from both the machines’ PLC and external sensors. We can use this data to:
- Determine conformity to quality requirements
- Identify performance gaps
- Check proper functioning
- Provide remote diagnosis and support
RapidDiag® can be used to solve isolated problems, or as a continuous process optimization tool. This internet-enabled device will even notify your maintenance department if a potential problem is identified, empowering your preventive maintenance approach.