"The strength of the Fives Group lies in its ability to combine the power of a Group of nearly 9200 employees with the autonomy of our more than 100 subsidiaries around the world. In terms of health and safety, the autonomy of each subsidiary in developing and implementing preventive actions is also accompanied by the individual responsibility of subsidiaries directors towards their employees, customers and partners."
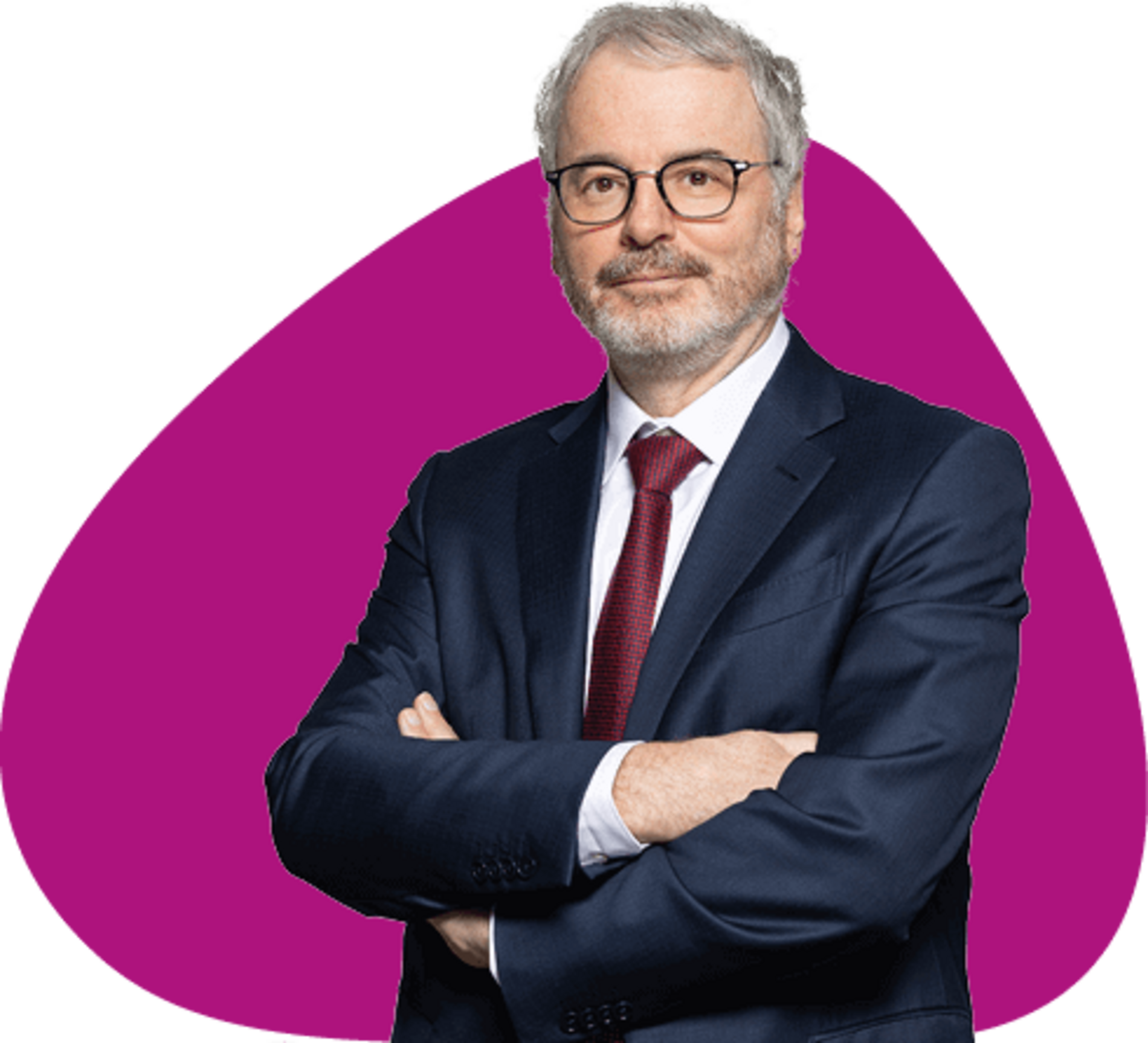
Frédéric Sanchez
2023 saw a sharp upturn in activity for the Group, which was accompanied by a rise in lost-time accidents and a return to the level of 2019, before the Covid period.
To achieve “100% Safety for All”, the objective of the Fives group, a roadmap has been rolled out. Today, priority will be given to incident prevention (detecting and dealing with risk situations) and training.
LTH & Safety Indicators | ||||
2019 | 2022 | 2023 | 2024 | |
Lost-time accident frequency rate (Number of lost-time accidents (≥ 1 day) x 1,000,000 / Number of hours worked) |
3,39 | 2,83 | 3,39 | 2,47 |
Severity rate (Number of lost days following an accident (≥ 1 day) x 1,000 / Number of hours worked) |
0,20 | 0,11 | 0,13 | 0,10 |
OUR AMBITION: GUARANTEEING 100% SAFETY FOR ALL OUR EMPLOYEES, CUSTOMERS AND PARTNERS
For us, working safely is more than a priority; it is a right and a duty towards our nearly 9200 employees as well as all our customers and partners in the 25 countries in which the Group operates.
All the subsidiaries of the Fives Group worldwide share a common objective: 100% safety for all our employees, customers and partners.
“Fives’ health and safety policy combines strong impetus from the Group with decentralised deployment, rooted in operational realities. Each subsidiary draws up an action plan tailored to its environment and risks and allocates the necessary resources. Knowledge of the field is the sine qua non of an effective health and safety approach.”
- Laetitia Liguori, Group Health & Safety Coordinator
This AMBITION is based on 3 PILLarS
Risk prevention, productivity and efficiency go hand in hand in the same quest for operational excellence. This vision means that prevention is at the heart of all our subsidiaries’ activities, whether in their projects, on their sites, in their offices or in their workshops.
INCIDENT PREVENTION
RAISING AWARENESS AMONG ALL EMPLOYEES AND TRAINING MANAGERS
INNOVATION THAT LEADS TO RISK PREVENTION
1. Incident PReVENTION
At Fives, we are developing a culture of risk prevention among all our employees. This is based primarily on detecting and dealing with risk situations that could lead to an accident in the working environment.
Every employee has a role to play in ensuring everyone’s safety!
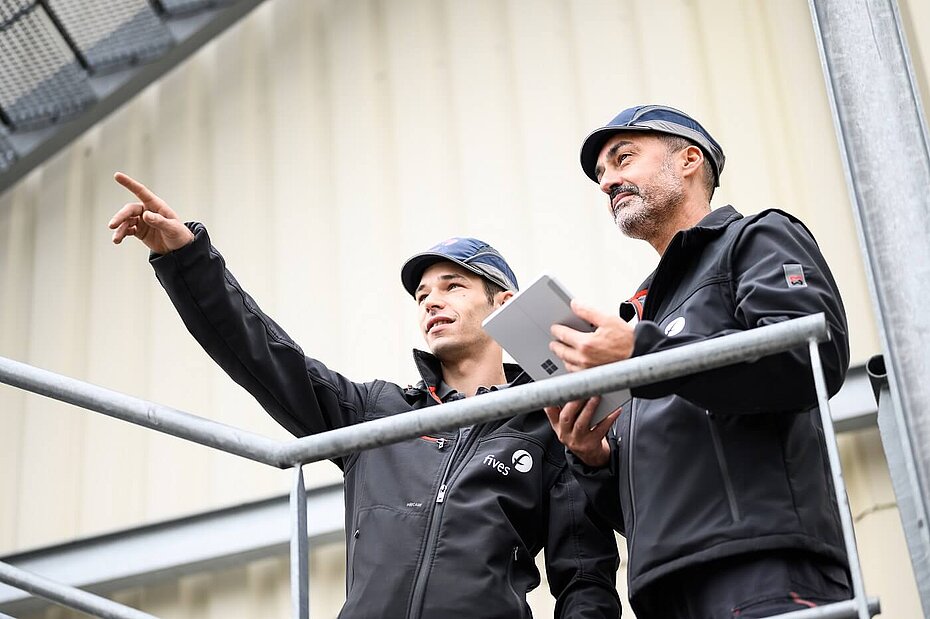
Safety Month
At Fives Syleps, we have introduced a safety month. It consisted of organising a major safety event (morning session for managers, safety flash meetings on dangerous situations, safety quiz). It ended with a team hunt for dangerous situations.
203 high-risk situations were reported, underlining employees’ commitment to 100% safety for all.
- Marie-Julie Leray Pereira,
Quality, Health, Safety and Environment (QHSE) Manager, Fives Syleps
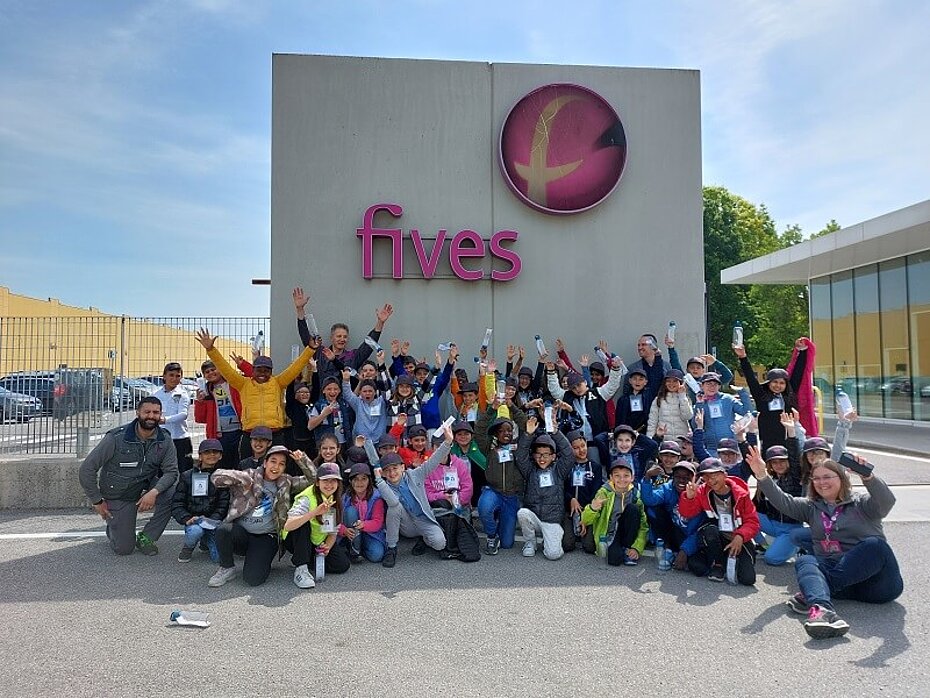
Role-playing games on safety
At Fives OTO, we organised World Safety Day with the local primary school. Role-playing games on safety were organised, with the protagonists being Fives OTO employees whose children attend the school. Over the years, we’ve seen that these initiatives raise awareness of the risks among children, but above all among parents, because explaining to their children or grandchildren how to work safely is like promising them that they’ll go home in good health.
- Filippo Bertolini, Quality, Health, Safety and Environment (QHSE) Manager, Fives OTO, Italy
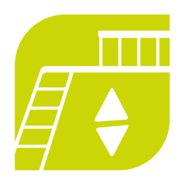
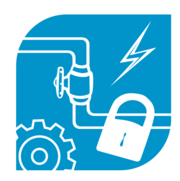
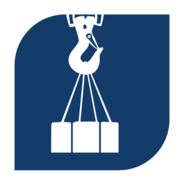
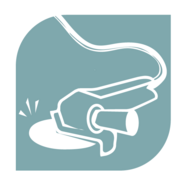
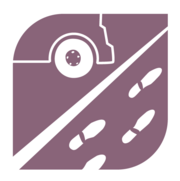

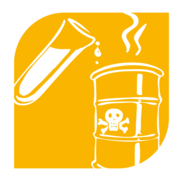
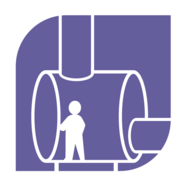
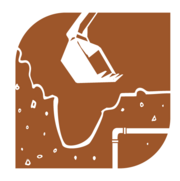
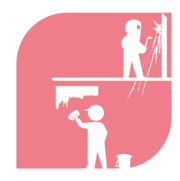
OUR 10 GOLDEN SAFETY RULES
The purpose of the Golden Rules of Safety established by the Group is to enable everyone to better identify and control the risks.
The Group’s 10 Golden Rules of Safety identify the 10 main risks that can cause accidents at Fives.
These 10 Golden Rules are deployed throughout the Group, and by subcontractors under Fives’ responsibility. Each subsidiary is also encouraged to develop its own awareness and communication initiatives and actions to ensure optimum local deployment.
2. RAISING AWARENESS AND TRAINING
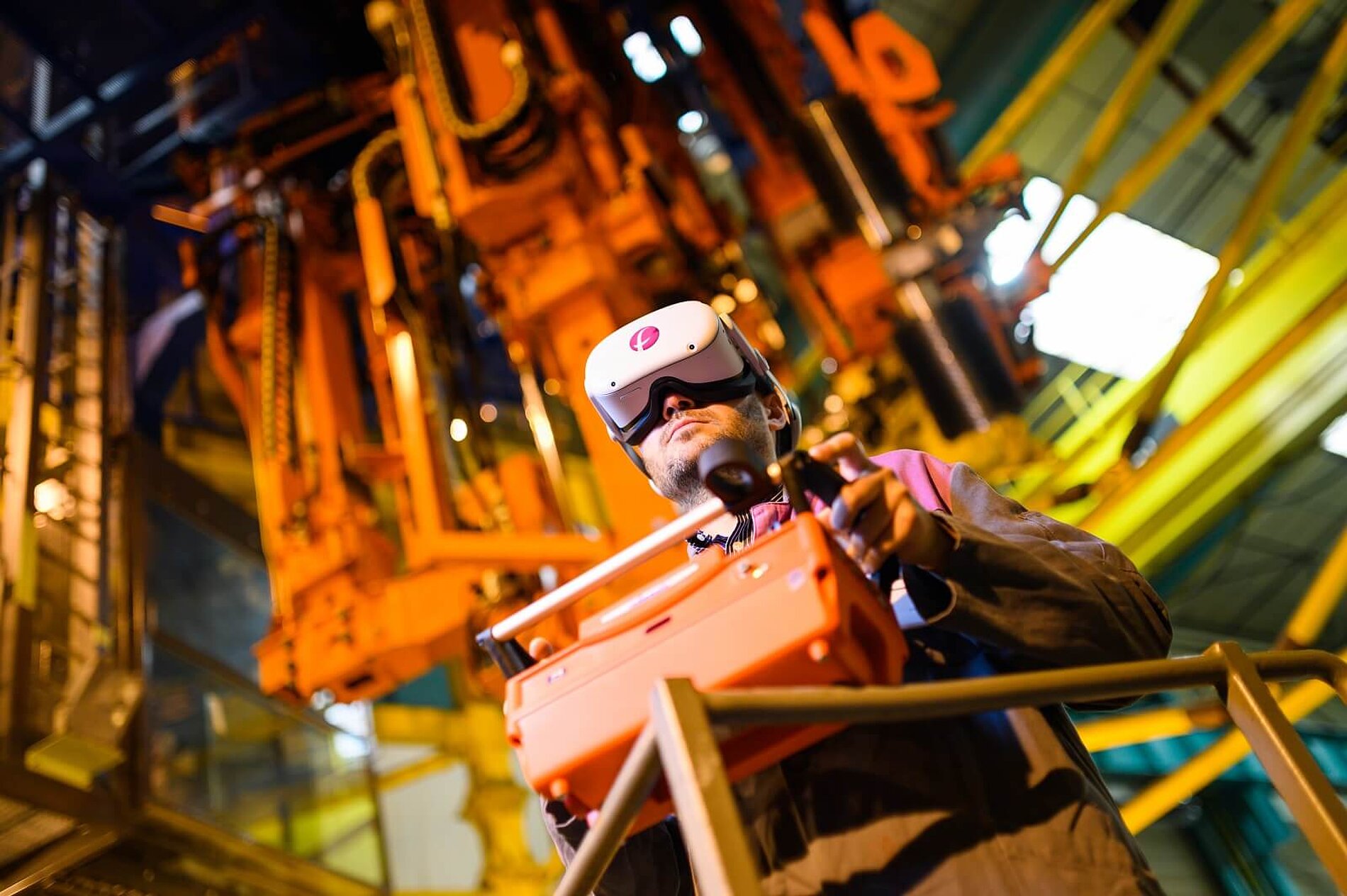
With our customers
- At Fives, our service activities are carried out directly on our customers’ sites. It is therefore our responsibility to work closely with them to ensure the health and safety of our employees.
Workplace Accident Feedback Reports
At Fives Maintenance, we have drawn up “Workplace Accident Feedback Reports” which we share with our customers so that together we can reflect on and commit to actions for improvement.
- Aurélie Morel QHSE Manager, Fives Maintenance
In our workshops & offices
- Raising awareness among our visitors: The safety rules to be observed on the site are presented to visitors via educational videos and/or directly by the Quality, Health, Safety and Environment (QHSE) Managers.
- Training our employees: In order to aim for 0 incidents, our subsidiaries regularly carry out awareness-raising and training programmes tailored to each division.
- Sharing information with teams : Regular communication is provided to teams on accidents and dangerous situations identified, as well as on the action plans put in place to guarantee 100% safety for all.
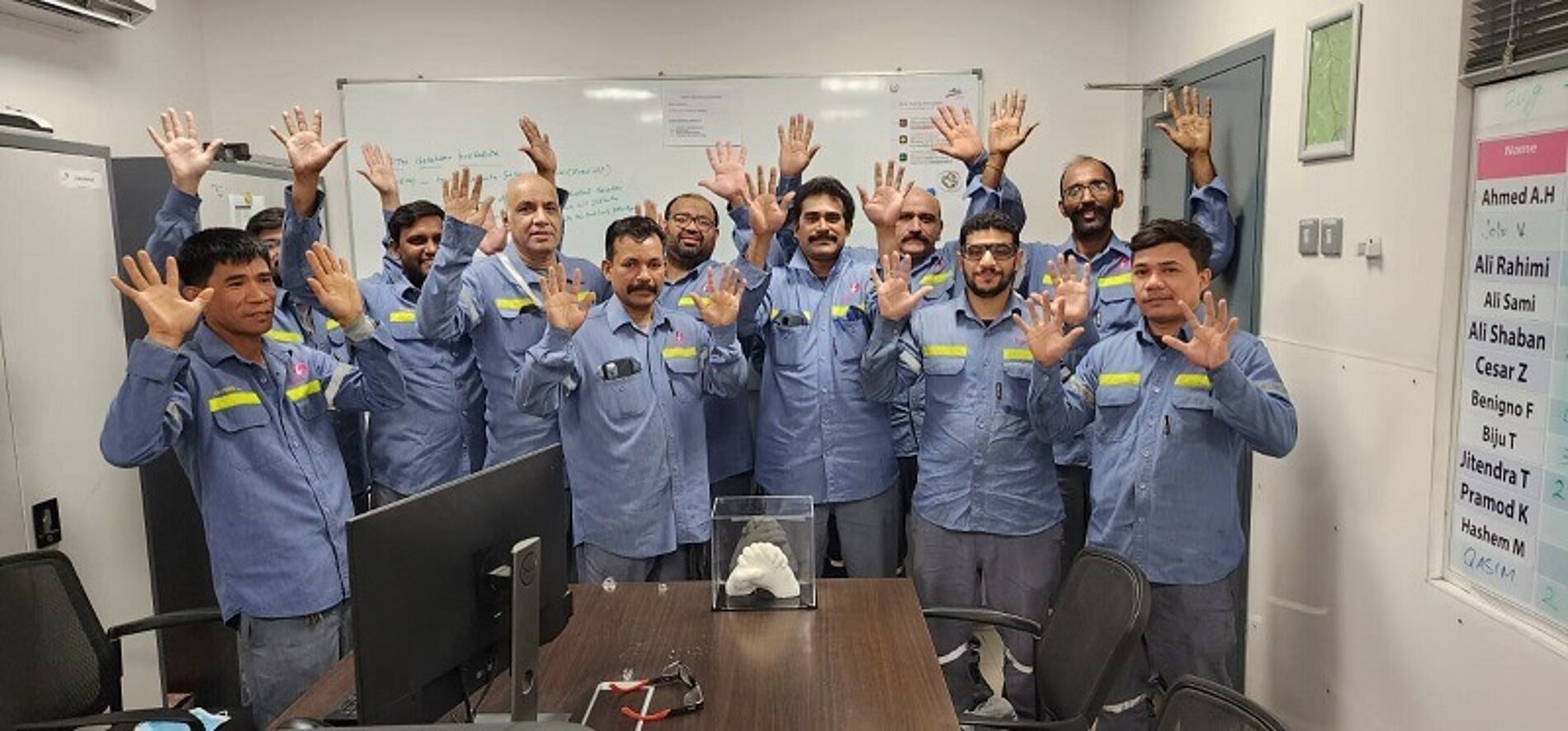
Hand Safe campaign
Fives Services Gulf is actively involved in the Hand Safe campaign, a global initiative to raise awareness of hand safety among all employees.
This campaign has been designed to provide them with the knowledge and tools they need to prevent accidents and injuries. We have set up a series of workshops, training sessions and awareness-raising programmes to mobilise all our employees.
- Hasan Qambar QHSE Manager, Fives Services Gulf
3. INNOVATION THAT LEADS TO RISK PREVENTION
Digital tools are used by the subsidiaries to facilitate the management of safety and strengthen the presence of managers in the field.
Purple Box
At Fives Maintenance, the PURPLE BOX tool has made it possible to:
- Increase the number of reports of risk situations (900 reports by 2023 compared with 300 before 2020),
- Facilitate the administrative work of the Quality Health Safety Environment (QHSE) engineers and provide better support for the sites,
- Guarantee traceability and efficient handling of events,
- Capitalise on and share the events that have occurred and the actions to be taken to secure all the sites and ensure 100% safety.
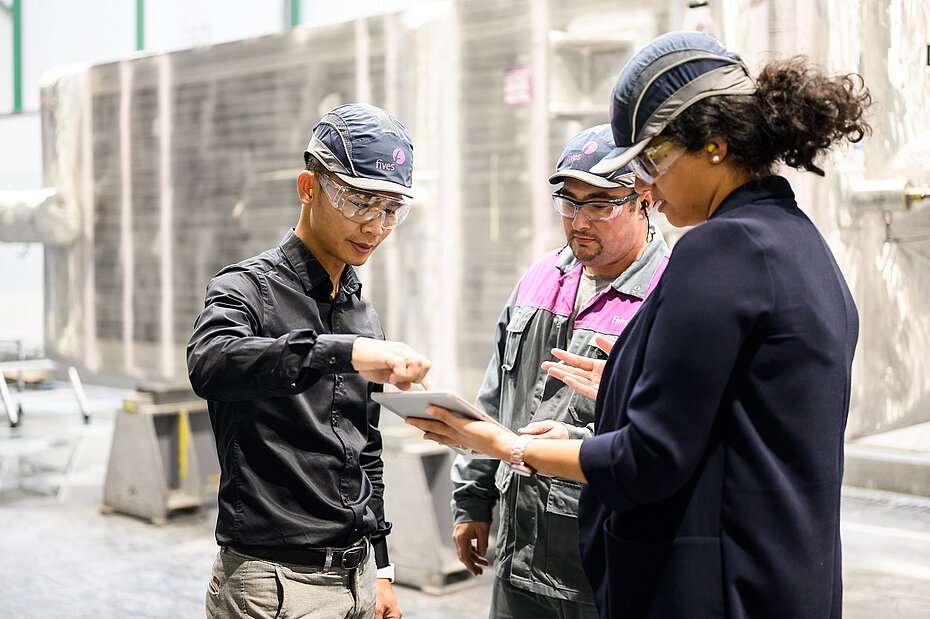
Monthly online training modules
At Fives Maintenance, to raise our employees’ awareness of risk prevention, we inform them (through talks, letters, etc.) about serious events that have taken place and also set up monthly online training modules.
- Aurélie MOREL, QHSE Manager, Fives Maintenance