Unlocking untapped potential of coil processing assets
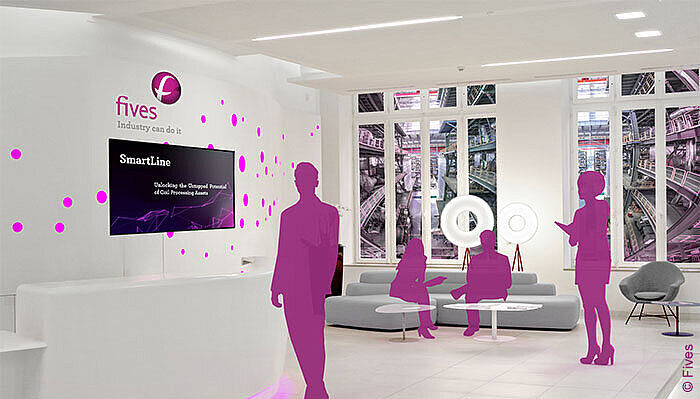
The three-day event hosted more than 300 industry leaders and experts who discussed priorities for steelmakers, technology and service providers, explored challenges across the steel supply chain and debated about the outlook for 2021.
Guillaume Mehlman, President of Steel & Glass at Fives, presented the SmartLine, a fully automatic control system based on predictive modelling, during the technology panel “Leveraging Advantage from Digital Technology”.
“You gave us a great example in your SmartLine - the way models can talk with each other and you can connect up information from the one end of the line to another – at what extend do you see the value of this development?” asked Richard Barret, Metal Market Magazine Editor, who moderated the panel.
“The SmartLine, implemented on the coil finishing lines at Marcegaglia’s Ravenna plant in Italy, has demonstrated real value after one year in terms of product quality and overall productivity,” explained Guillaume Mehlman. “We had a very unique and practical approach based on domain knowledge and physical models while developing the fully automatic solution, which delivered real results to the plant.”
Aldo Fiorini, Plant Manager of Marcegaglia Ravenna added, “Implementation of the SmartLine allowed us to reduce direct costs through energy saving, increasing productivity, production flexibility and general quality improvements, such as:
- 5% of productivity increase (line speed)
- +/- 10°C soaking temperature uniformity
- +/- 15MPa tensile strength uniformity
- 25% reduction of coating variability
- 25% dross reduction”