Introducing COAST: Composite Optical Automated Surface Tracking
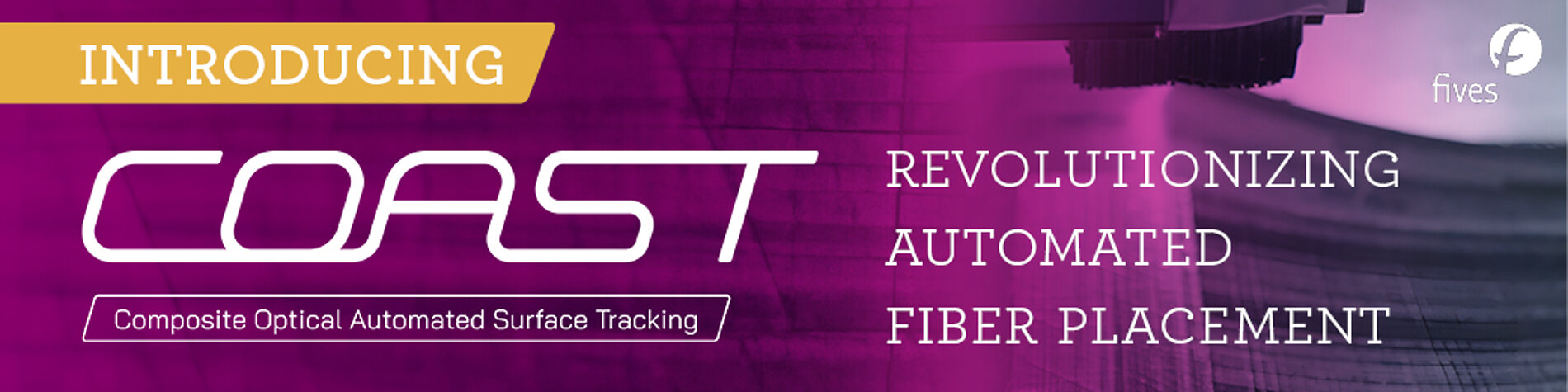
Fives, a global leader in industrial engineering solutions, is proud to announce the launch of its innovative In-Process Composite Inspection technology, "COAST: Composite Optical Automated Surface Tracking." COAST represents a significant breakthrough in the field of Automated Fiber Placement (AFP) by enabling precise measurement and defect detection on contoured composite surfaces.
COAST is the world's first composite measurement technology proven to be statistically capable of measuring process defects in Automated Fiber Placement, including gaps, twists, tow end placement, and missing tows, on complex contoured surfaces.
This cutting-edge technology leverages Optical Coherence Tomography (OCT), a laser-based technology adapted from the medical industry, to create highly accurate surface profiles during the AFP manufacturing process. These surface measurements are seamlessly integrated with machine position data, computer-aided manufacturing (CAM) data, and advanced computer vision algorithms to detect process defects in real time.
Automated Fiber Placement involves intricate mechanical processes, making it susceptible to variations. With components such as rotating mandrels, malleable materials, heavy end effectors, and multiple axes of motion, continuous monitoring is essential to ensure that AFP products meet design specifications.
While existing technologies like Line Laser Triangulation (LLT) have shown promise for planar composite surfaces, they fall short when it comes to detecting defects on contoured surfaces. COAST bridges this gap by introducing OCT technology to composites, maintaining superior signal quality even as AFP machine heads rotate to fabricate contours.
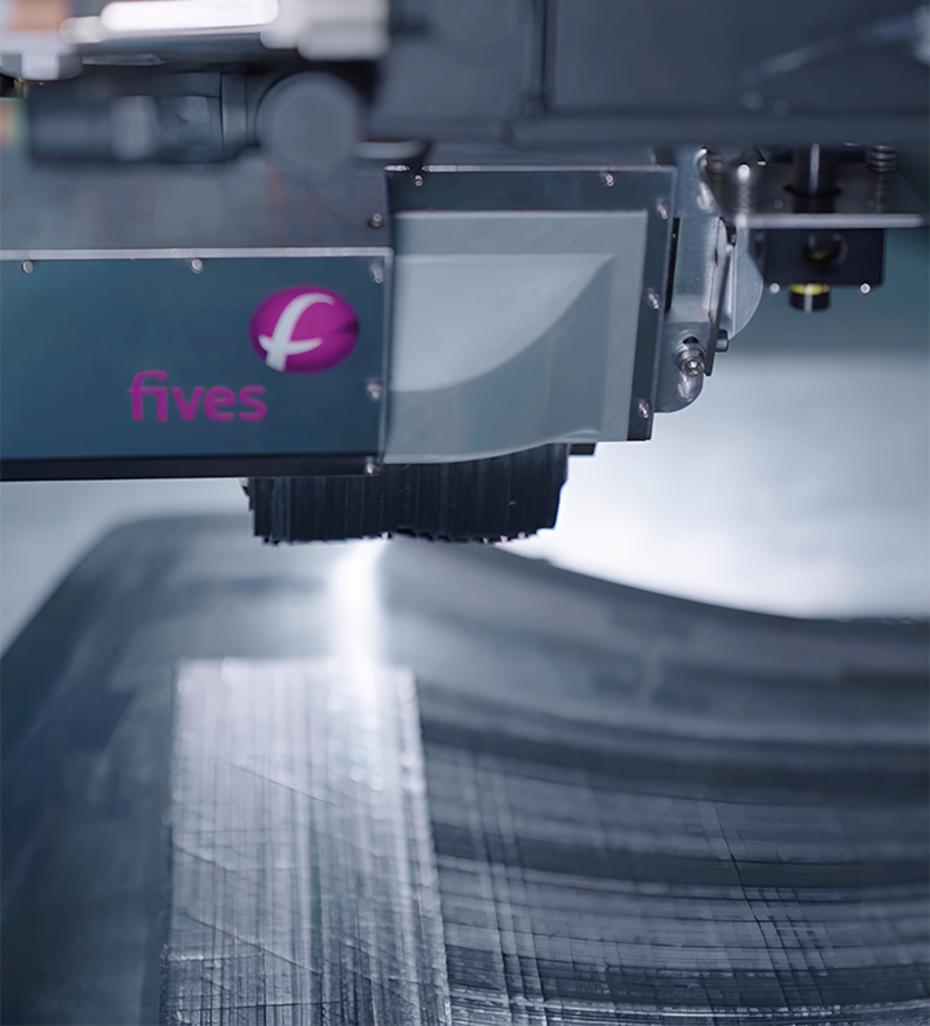
One of the standout advantages of In-Process Inspection technology is evident in the signal quality comparison during machine head rotation. When an AFP machine head rotates 20 degrees to create a contour, the LLT signal degrades from 100% quality to 78%, whereas the OCT signal only degrades from 99% to 95%. This signal quality difference becomes more significant with increased machine head rotation, demonstrating the superior performance of COAST.
The precise 3D point cloud generated by COAST serves as input for defect detection algorithms, enabling AFP manufacturers to monitor process variability and identify the probability and location of material defects like never before.
Before the introduction of COAST, manual inspection was the industry standard for composite quality control. While effective, manual inspection relied on human operators and lacked the ability to capture detailed data over extended periods, introducing additional variability into the manufacturing process.
COAST addresses these limitations by automating data collection and quality analysis throughout the part's lifecycle. In the design phase, designers receive instant, detailed feedback on prototypes produced by AFP machines, facilitating rapid iterations and optimal parameter discovery. During production, manufacturing engineers gain continuous feedback on surface quality and defect locations, ensuring the health of their process.
In June 2023, COAST was successfully deployed in a customer facility, demonstrating its ability to allow operators to assess process defects more quickly than manual inspection techniques. Further enhancements to the user interface are on the horizon, with a projected 90% reduction in inspection and rework time by 2024.
COAST is poised to transform AFP quality specifications, shifting from a ply-by-ply approach to a holistic 3-dimensional perspective. This new perspective, made possible by In-Process Inspection technology, aligns composite quality more closely with the true physical properties of the material under study.
Additionally, COAST will drive the widespread adoption of AFP by increasing Overall Equipment Effectiveness (OEE). Preliminary assessments show that
OEE can increase by 30% with the full integration of In-Process Inspection technology, translating into a significant cost reduction for AFP end-users.
The COAST '1.0' product is currently available for integration into any Fives AFP machine, with discussions underway to integrate it into third-party AFP machines. Ongoing research and development efforts aim to expand the system's data collection capabilities and acquisition rates, addressing the evolving needs of the AFP industry.
The success of COAST is the result of two pivotal collaborations. Fives partnered with the Canadian National Research Council (CNRC) to integrate OCT technology into AFP machines. This long-standing partnership has yielded significant advancements in sensor development.
Another essential collaboration involves a current customer who has extensively tested and adopted In-Process Inspection technology. The collaboration has resulted in a tangible reduction in inspection time and increased workflow efficiency.
Fives is committed to advancing manufacturing technology and enhancing the quality and efficiency of AFP processes with COAST. This groundbreaking technology promises to reshape the industry by enabling higher precision, reducing costs, and increasing the accessibility of AFP manufacturing.
For more information about COAST and Fives' In-Process Composite Inspection technology, please visit Fives – Composites & Automated Solutions or contact our dedicated specialist.