Landis pioneered orbital grinding, or “pin chasing”, technology in the grinding industry. This established a new standard of precision and flexibility to the finish grinding of camshafts/crankshafts, and other non-concentric applications. This technology is applicable wherever your grinding applications require high-speed interpolation and high stiffness.
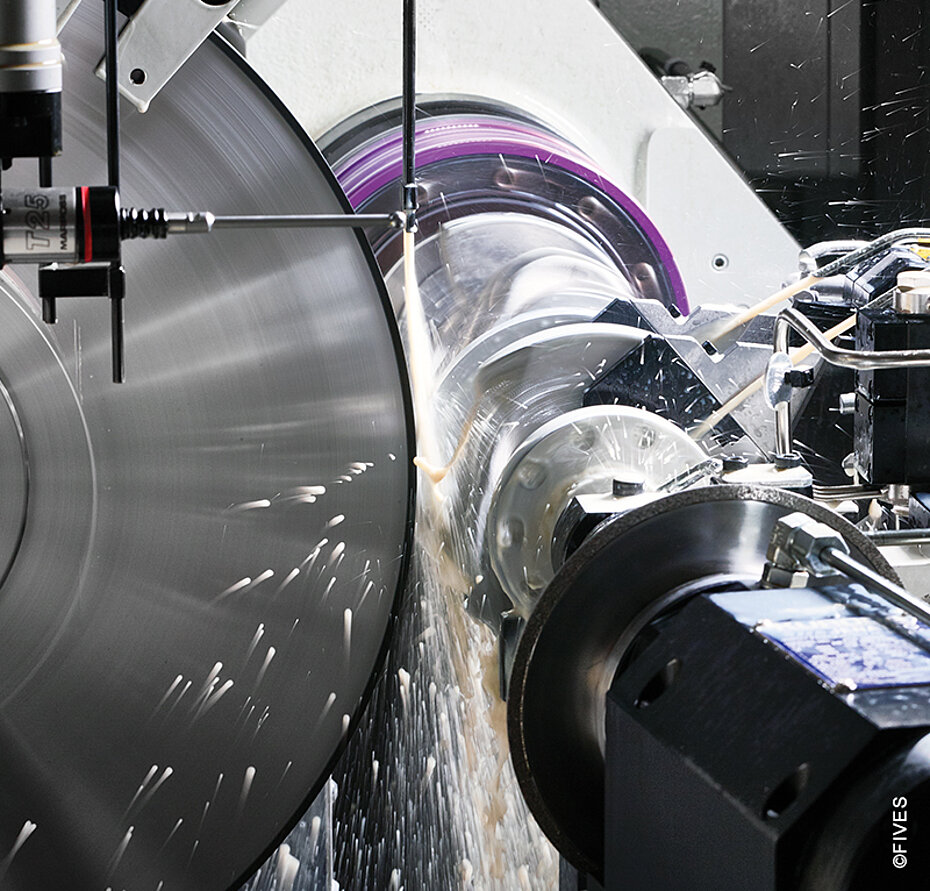
robust and reliable machine solutions
Our range of solutions provides optimized grinding of crankshaft pins and journals and camshaft lobes and journals to non-concentric components. Workpieces range in size, from small to large sized components up to 8.5m in length for heavy industry, marine and energy applications. Additionally, our orbital machines can use either CBN or conventional wheels.
Our commitment remains consistent. We provide our customers with the flexibility, precision and performance that guarantees the highest quality. Our robust and reliable machines can be configured to your specific process and production needs.
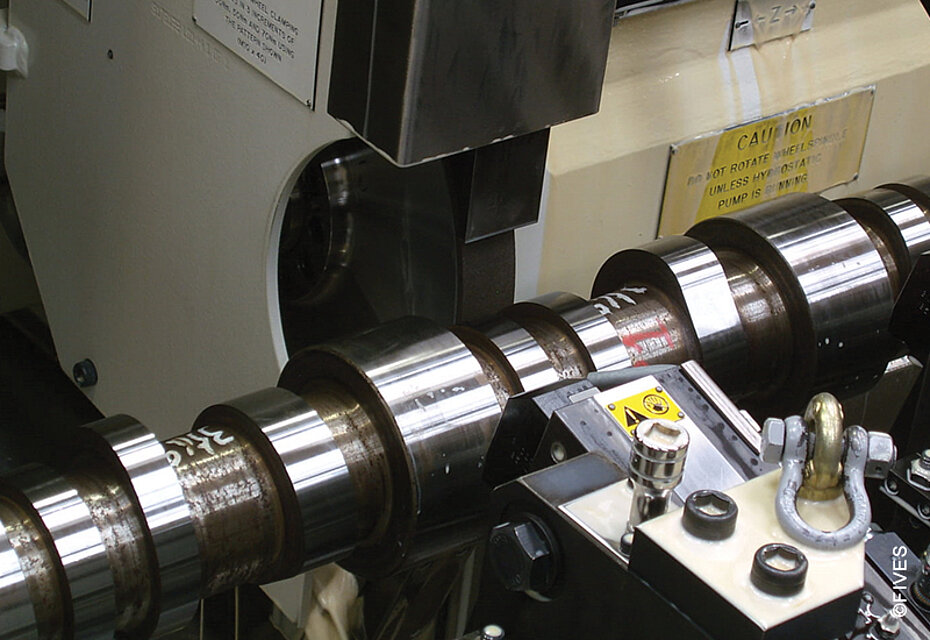
Orbital grinding of small to medium applications
Our high-volume, precise and flexible Landis machines set the benchmark for grinding applications up to 1,500mm long. Incorporating the technology of larger machines into a small footprint, we have amplified through-put, improved cycle times and maximized production levels.
Landis LTC1e Landis LT1Se/LT1Se-DH Landis LT1e Landis LT2e
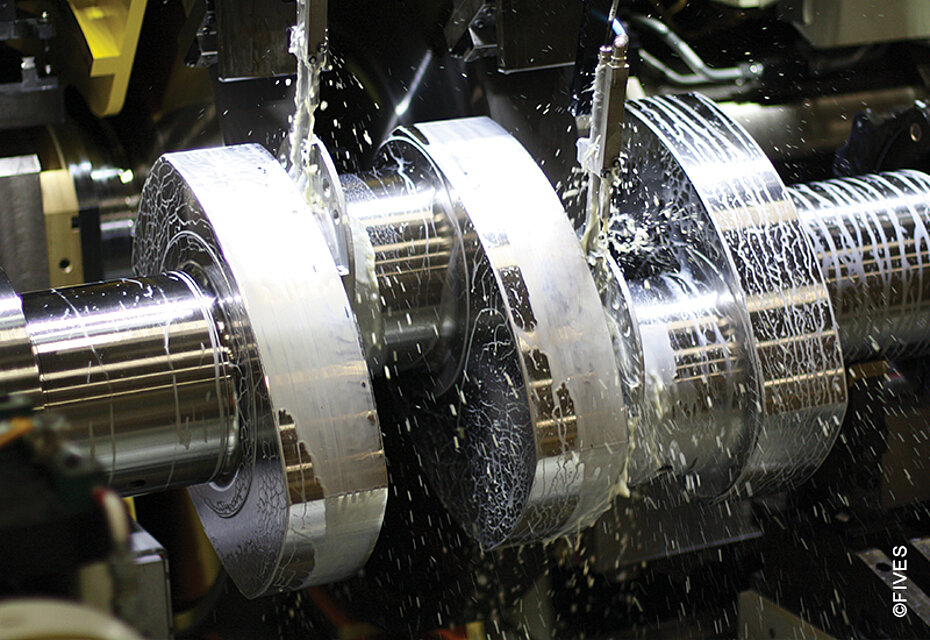
Orbital grinding of large applications
Our line of large orbial grinders caters to components up to 8.5m long for heavy industrial, locomotive, marine, truck or aerospace applications. Along with single or twin wheel heads options available, Landis brings the latest developments in high volume grinding through our patented grinding processes. Additionally, our industry leading Landis machines offer high precision, flexibility and reliability, including reducing scrap.
Landis LT2He Landis DuoFLEX Landis LT2HHe Landis LT3e
Interested in a precision location tool that allows uniform stock removal?
Our MicroLocate innovation enables simple and efficient finish grinding of new and remanufactured large crankshafts with a precision location tool that allows uniform stock removal. With improved location accuracy, you can save money and improve efficiency in your finish grinding operation.