LEVERAGING ARTIFICIAL INTELLIGENCE FOR PROCESS OPTIMIZATION
As part of the CortX Alchemy platform by Fives, we have developed a nine-step approach and a full set of tools that enable us to collect data on the way machine processes are carried out. Our artificial intelligence (AI)-based tool set runs a deep analysis of process performance. Essential in this approach is the need to control all factors affecting quality. By searching for and identifying these most influential factors, we can ensure quality repeatability.
Using our methodology, we then can optimize that performance by determining where improvements can be made, so problems can be identified before they occur. This leads to a vast improvement in terms of overall system quality.
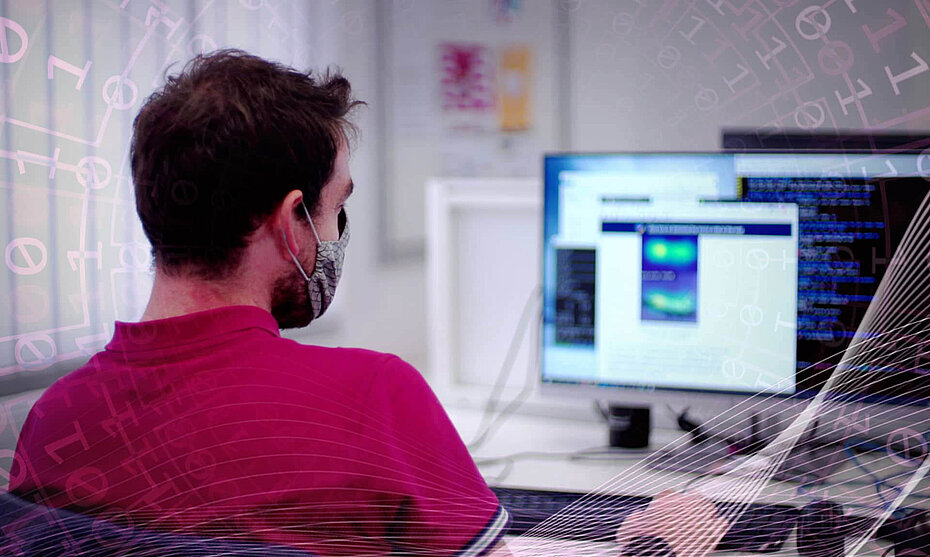
TAKING A DEEP DIVE INTO DATA
At Fives, we place data at the core of all our activities to improve our clients’ operations. From data analysis to data engineering through to building AI models based on that data, our tried and true methodology has been developed to influence product quality.
Our goal is not simply to provide an out of the box solution to our clients. Every solution and service we offer—from quality improvement to predictive maintenance to industrial vision— is tailored directly to each specific client. We want to accompany them along their entire value chain journey from the moment they set up or redesign a facility to its end of life.
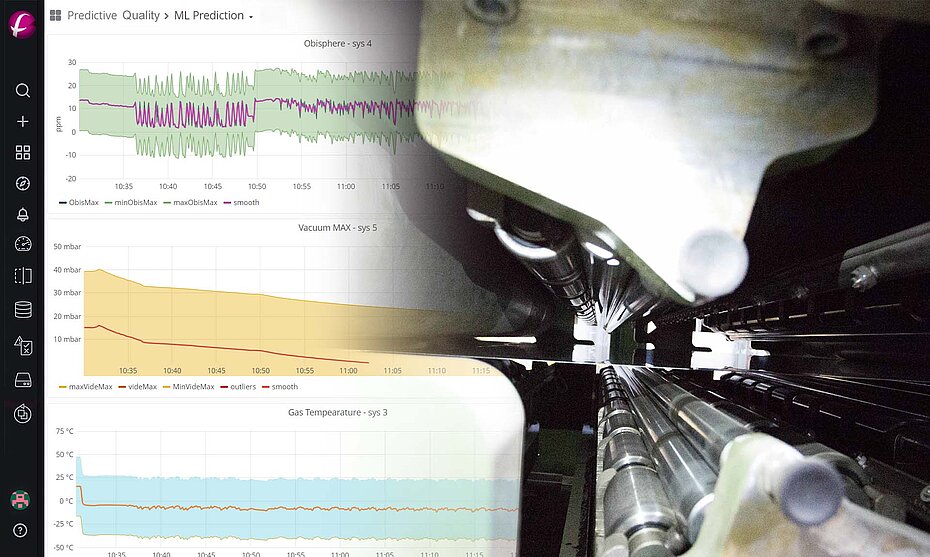
REDUCING PROCESS ISSUES THROUGH TIGHT MONITORING
With the knowledge and understanding derived from our analytics, predictive maintenance and vision expertise, we can help our clients create a continuous optimization pattern for their equipment and processes. The goal is to strengthen how operations are driven, while making it clear to end users how processes can always be made more efficient and effective.
In this way, we can optimize the repeatability of positive actions while diminishing error-laden processes. This is the role of our tools and the underlying objective for all Fives strives to accomplish.
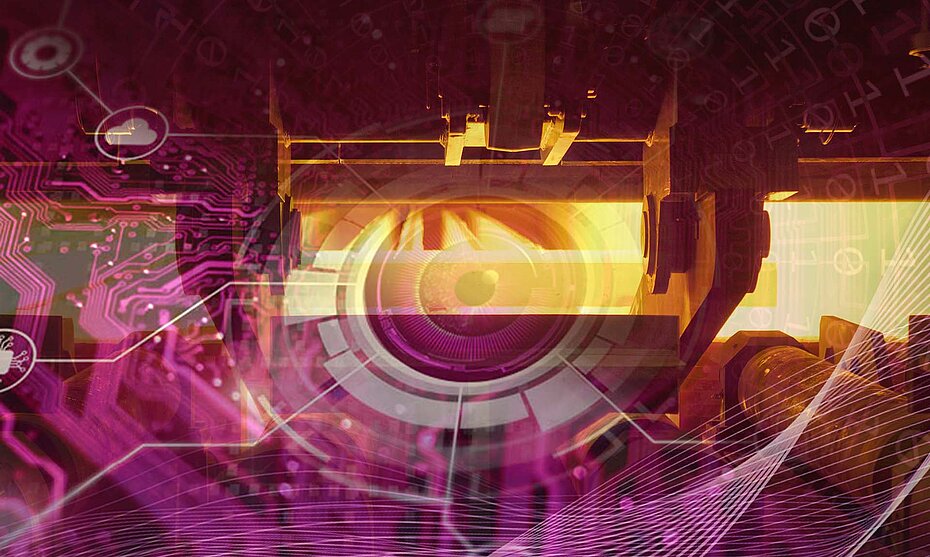
GETTING PREDICTIVE WITH INLINE MODELS
We aim to provide industrial operators with the opportunity to continuously improve their facilities. That means giving them the proper inline models that will enable continuous monitoring of process parameters. Controlling these most influential factors leads to a system’s overall improvement.
Our solution integrates these predictive models into their activities, constantly alerting operators, guiding them toward ways to adjust their processes to better improve their market competitiveness. Gathering massive amounts of accumulated data, our inline models can then inform the computers how to improve upon an operation. These models work in parallel with actual machine steering computers to analyze production quality.
We can also help clients get to the root cause of a problem, showing them the best way to fix it, and then find a way to automate that fix for the future.