Increase the productivity of your high-precision machines with engineering modifications from Fives. As an OEM specializing in high-precision machines, we have the skills and tools you need to improve machine performance. Optimize productivity, reduce downtime, and improve part quality.
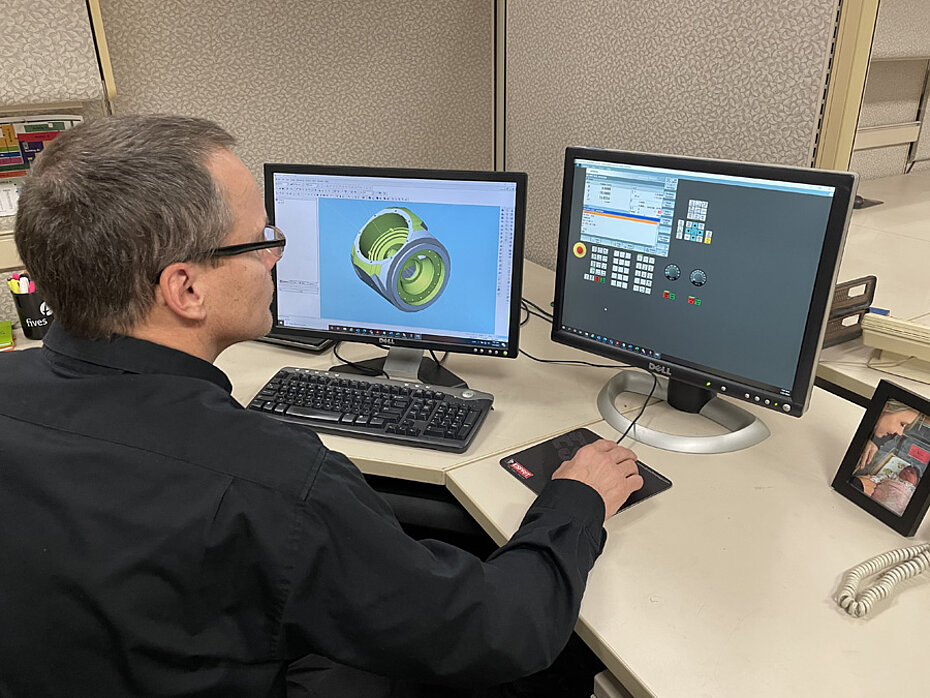
Save money and improve performance with engineering modifications
Machines lose performance over time – but that doesn’t mean they have to be replaced.
Metal removal rates may decline over time, slowing productivity and reducing part quality. But these issues can be remedied with appropriate engineering modifications.
Our modernization and maintenance solutions enable you to increase machine performance at a fraction of the cost of replacement.
Cut downtime, save money and improve performance. With more than a century of experience and an existing inventory of ways, racks and bearings, we can boost feed rates and machining speed and return your machine to OEM specifications. In fact, many of our solutions have enabled our customers to exceed original specs.
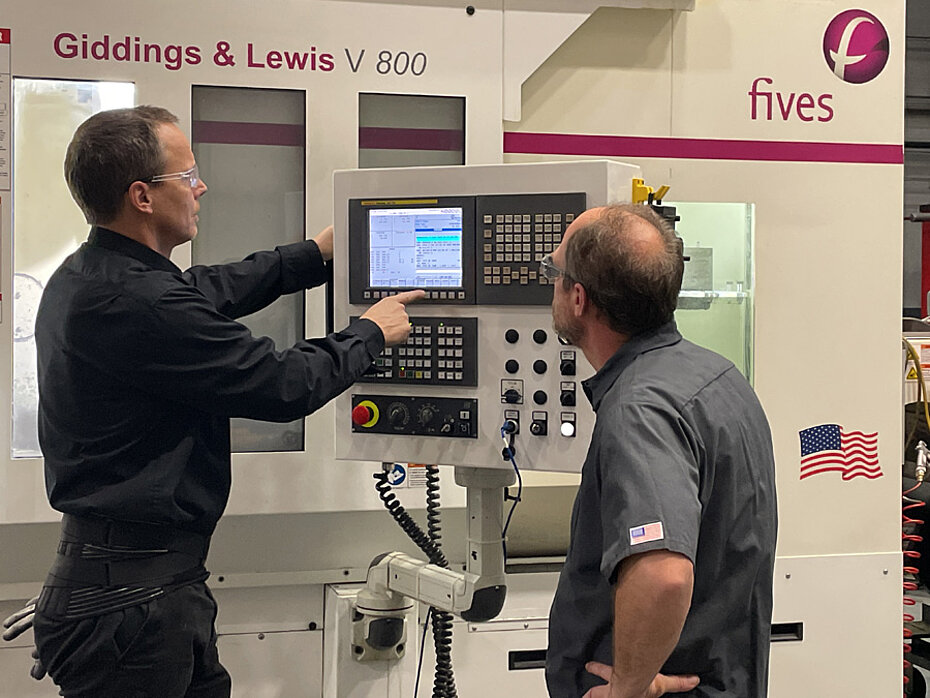
Complete machine solutions
From new spindle technology to control retrofits and gearbox rebuilds, we offer a full range of engineering modifications to boost machine performance. We work with you from the earliest planning stages right through to implementation and beyond to make sure you get the results you need.
- IP backed solutions
- Ti spindle carrier retrofits
- Anti-drop systems for maximum safety
- Automatic tool changing systems and robotic tool changers for improved productivity
- Removable spindle inserts
- Removable wear strips
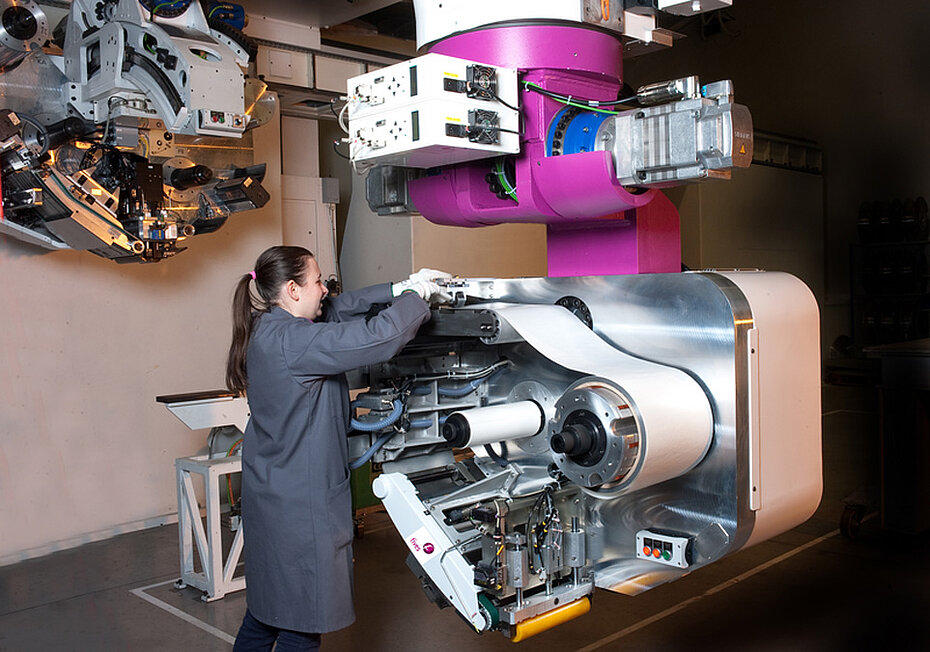
Case Study
Challenge
Carrying out the following modifications to reduce downtime and bring the machine up to performance for a customer.
- Siemens 840SL Control Retrofit
- State of the art Fives Cincinnati Ti Spindle Technology
- HSK125 Tool Interface
- 150KN Drawbar Holding Forces
- 2200 Nm Torque, 3,500 RPM
- New hydraulic chiller system
- Rebuild gearboxes
- All way and bearing replacement
Results
- Instant 17% productivity improvement due to bending moment capability
- A ~30% reduction in the average part program cycle time
- Downtime reduced to less than 1%
Proof of excellence
The customer was so satisfied with the results they requested the same scope of work to be completed on two additional machines.