From spare parts to revamp projects, from training to production support, Fives is ready to help you get the most out of your glass manufacturing. We focus on efficiency and flexibility to enhance the capabilities of your teams and optimize production.
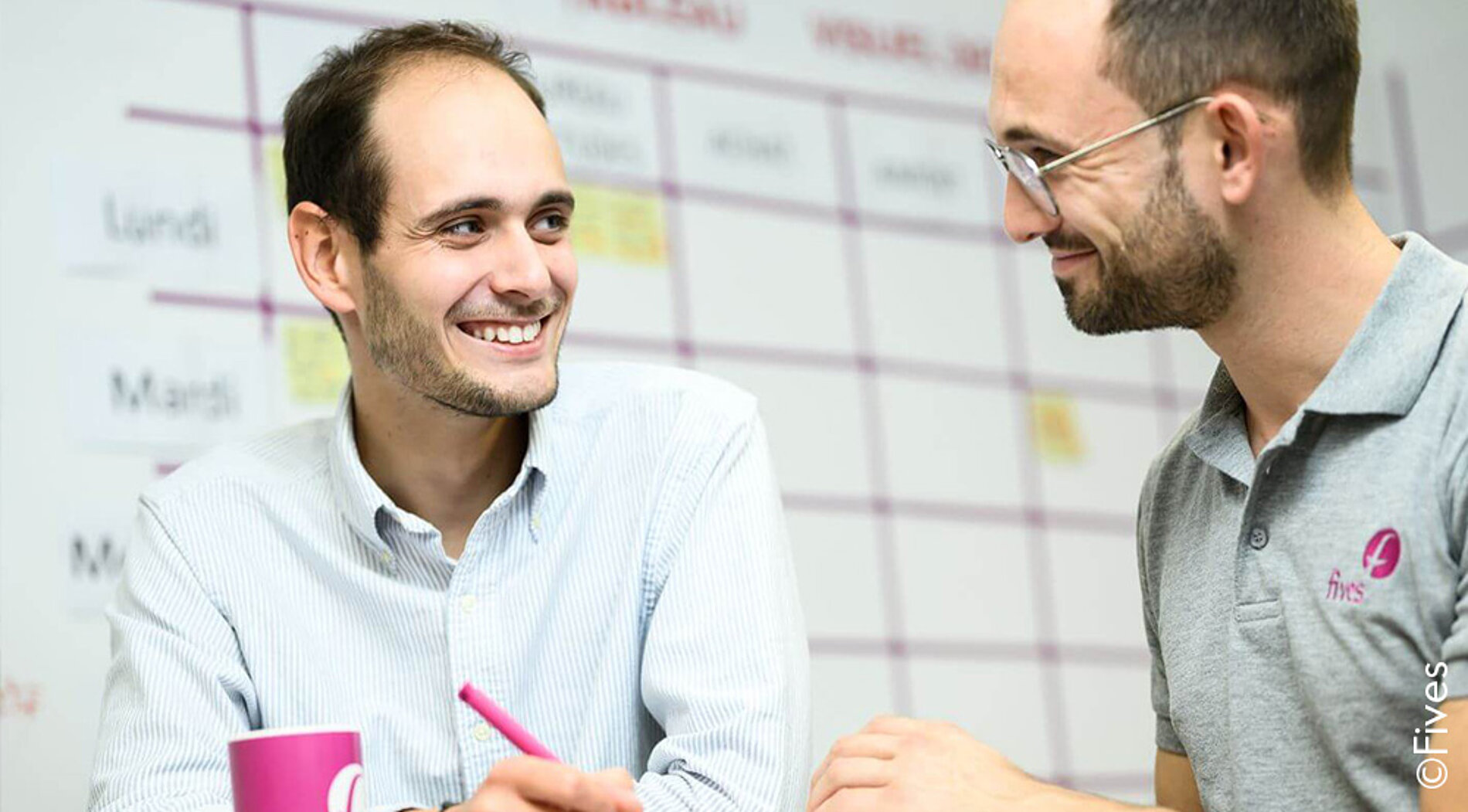
Expert training programs
Two ranges of expert training programs:
- Management – For future operational managers in the fields of production, quality, maintenance and plant management.
- Expertise – Train candidates to a high level of expertise to ensure that you have in-house experts as your organisation evolves.
Our training applies to both our own proprietary hot-end equipment and that of other suppliers. It can be conducted in the utmost confidentiality and can be completed in modules.
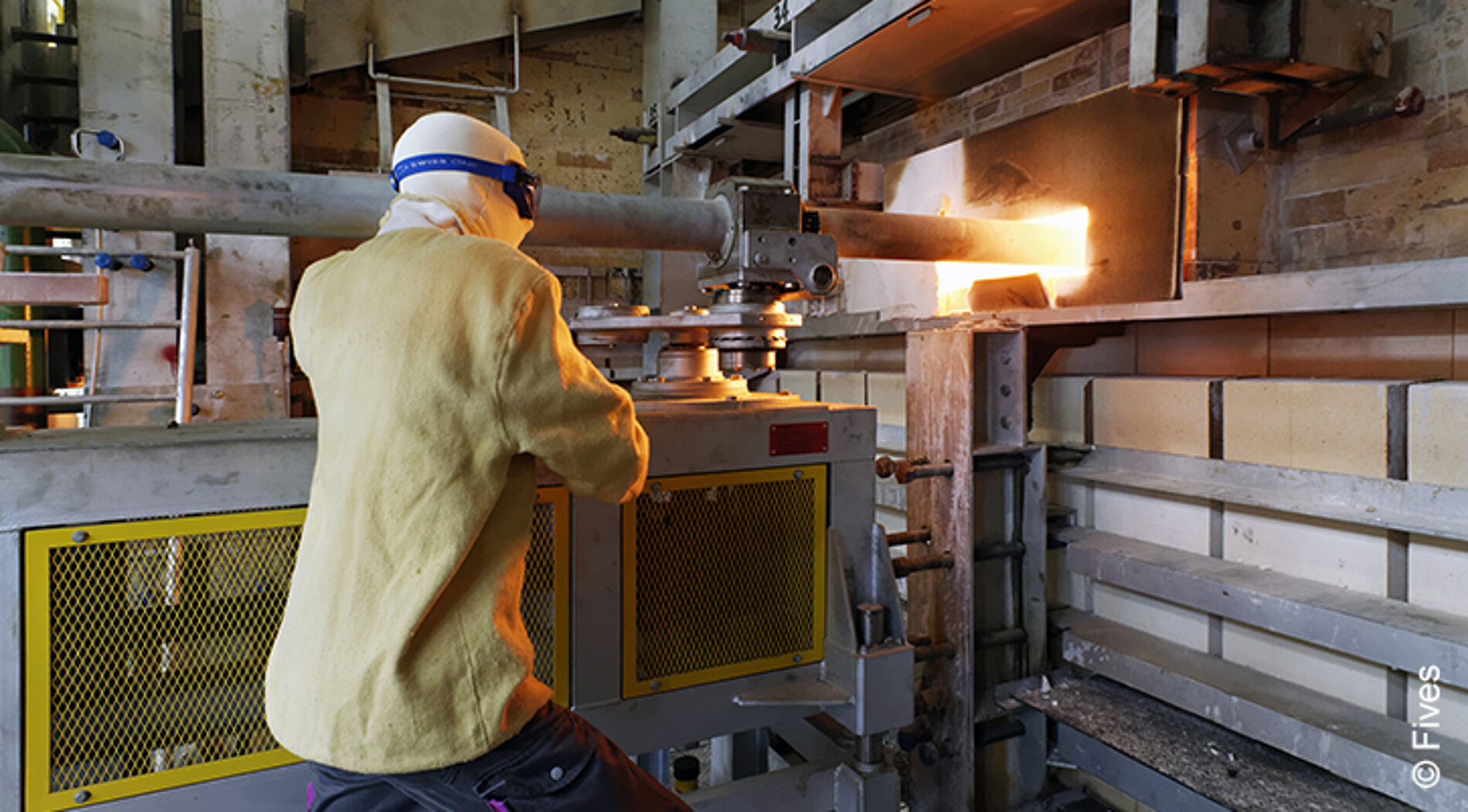
Production assistance
We can provide on-site or online production assistance in the following areas:
- Technical support during a quality crisis
- Preparation of line maintenance operations
- Suggestions for modifications in the installation to quickly improve productivity
- Definition of parameters for new products
For example, if you experience edge distortions or want to improve cutting, we cand either send the experts to your site or provide remote support.
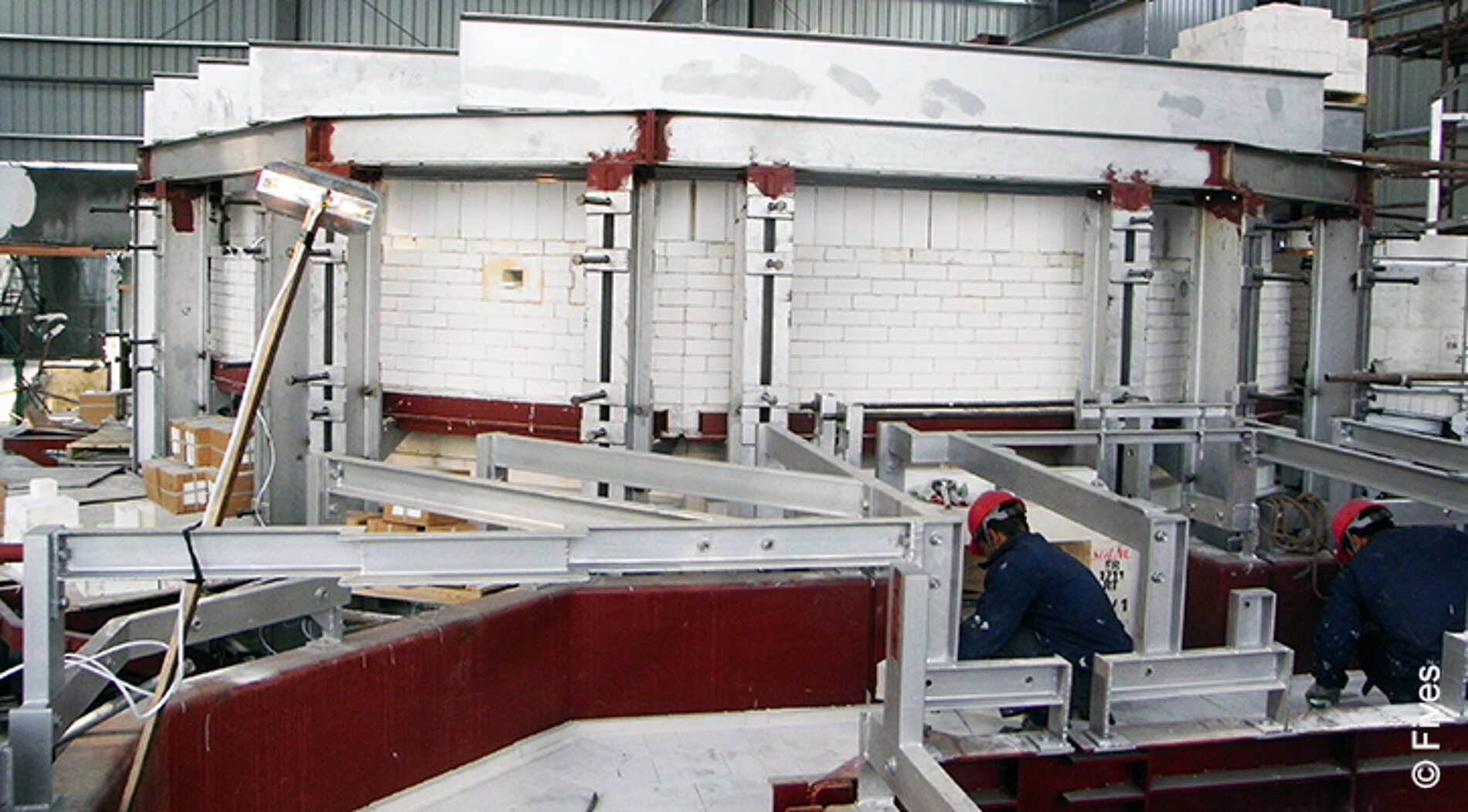
Revamping
Full support for upgrades and modernization to:
- Increase production
- Produce new glass colours, new quality and new grades
- Improve production quality
- Reduce operating costs
- Improve equipment reliability
- Increase energy efficiency
- Reduce environmental footprint
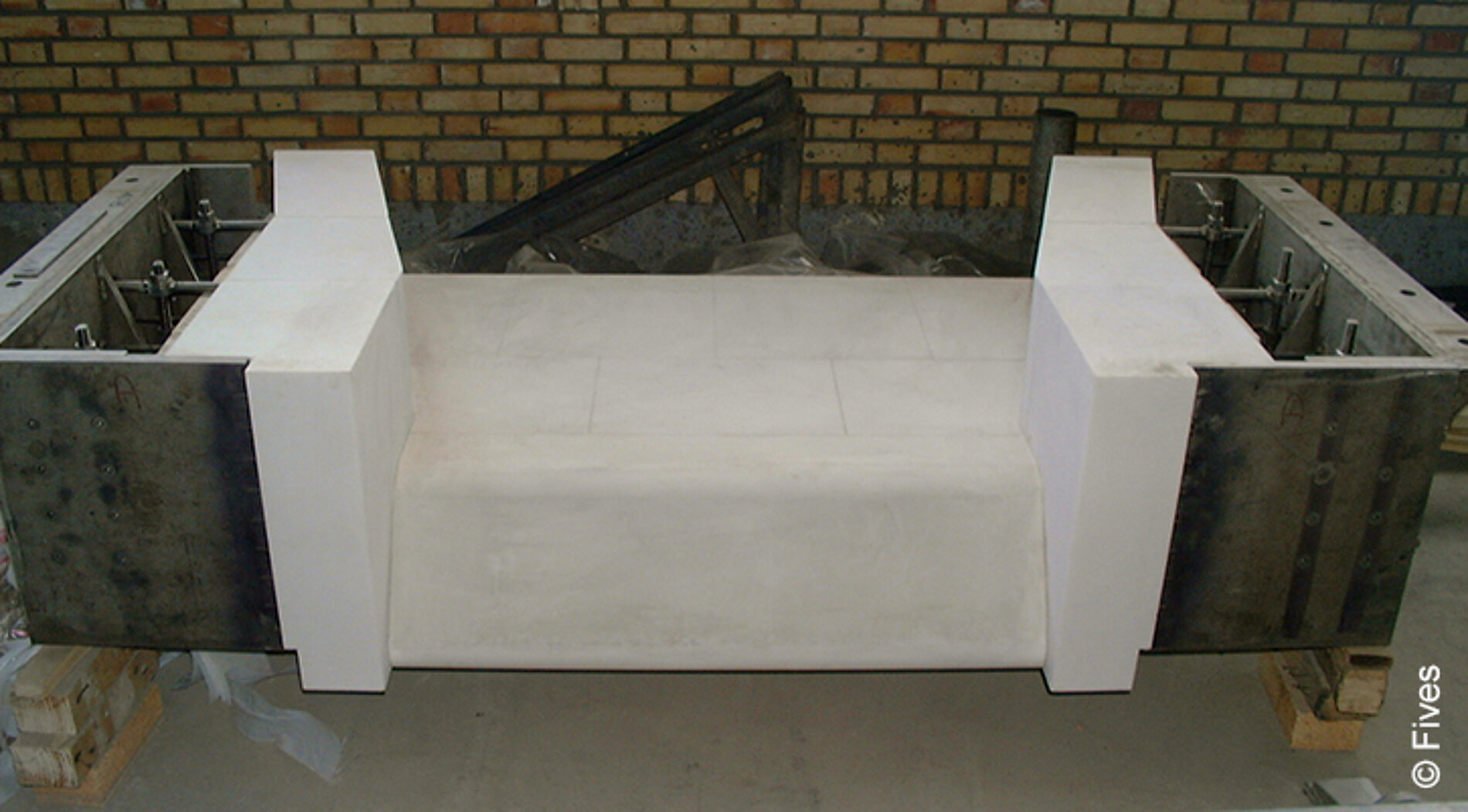
Spare parts
We are committed to provide proactive after-sales services:
- Genuine high-quality spare parts
- Guaranteed Original Equipment Manufacturer spare parts
- Up-to-date spare parts in line with the latest technological development
- Solutions for the best performance and easy operation
- Maximum availability and reliability throughout the entire equipment lifecycle
- Range of parts with predefined prices and conditions
- Comprehensive preventive maintenance work services