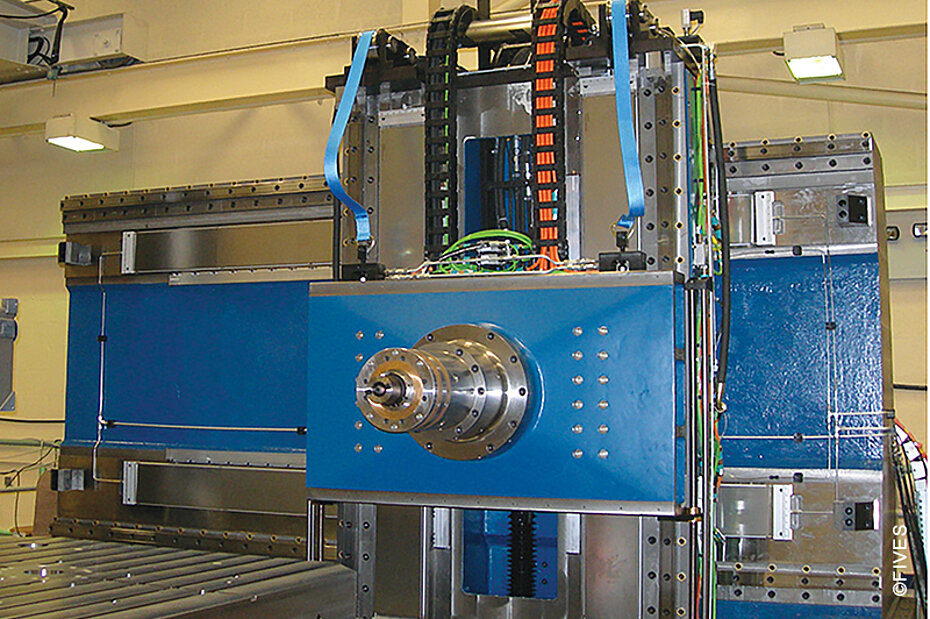
THE PROBLEM
On many large machine tools, the performance of the vertical axis is often the limiting factor in the accuracy of the machine. Traditional ball screw methods have inherent backlash and a limited life. For large axes, a counterforce mechanism will be required. Pneumatic and hydraulic methods are used, but these are expensive, complex and all introduce hysteresis to the axis. Therefore, a new counterforce design was needed to allow higher speeds and accuracies, better dynamic performance, reduced mass and cost – particularly important where linear motors are desired.
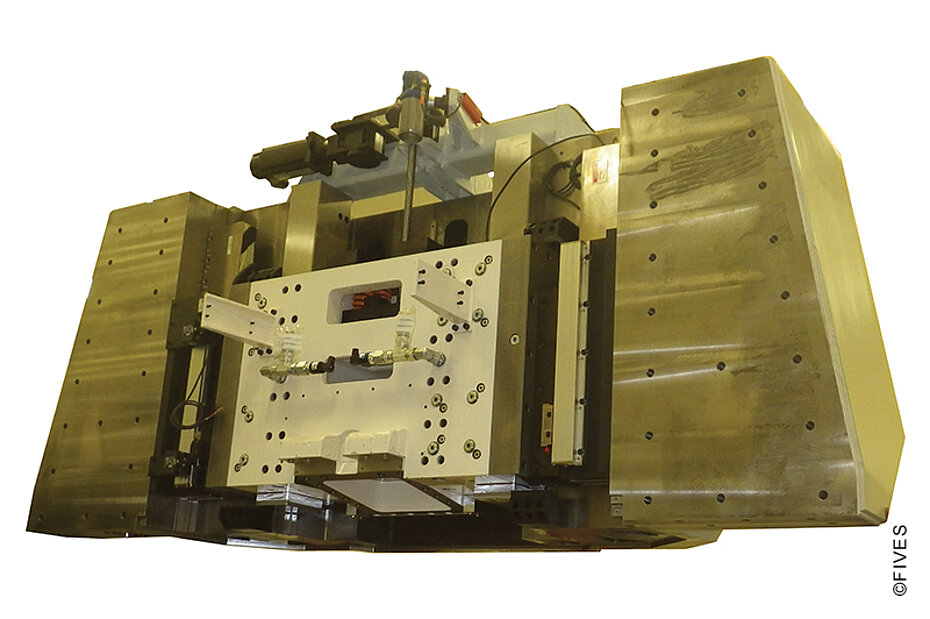
THE SOLUTION
Using CAD, FEA and test rigs, a new counterforce mechanism was designed. A slave axis uses a traditional ball screw to support the mass of the carriage but is mechanically decoupled from the carriage itself, through a spring system. For the master axis, linear motors and high resolution linear encoders are used to drive and position the axis, for high accuracy positioning. A position demand is sent to the master axis, simultaneously ‘followed’ by the slave axis to provide a counterforce to the carriage mass.
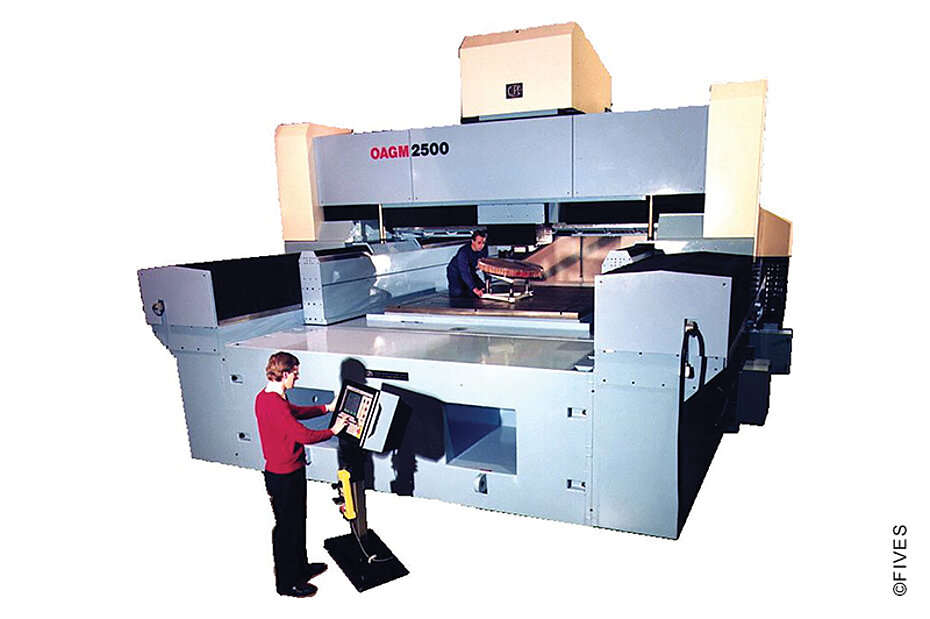
the result
- A patented, high accuracy, high speed, counterforce solution for large axis mass
- Successfully implemented as an upgrade to existing customer machines, 25 years after the original machine was installed. As well as new, large optics grinders with freeform capability and sub-micron positioning accuracy
Check out our Engineering Partnership brochure to learn more about our available offers.