Our high velocity, RAM-effect, low-NOx burner
Fives’ North American HiRAM® industrial burner combines large capacity with high velocity. The burner improves heat transfer by reaching parts of the load that radiation cannot "see", and standard low velocity burners do not penetrate. True high velocity results from the North American HiRAM®’s exceptionally high Btu/h input rates and are relative to its reduced tile discharge area. This burner technology is best used in applications like aluminum melting, heat treat furnaces, drying, air heating, forging, incineration, ladle heating, dryers, calciners, and roasters.
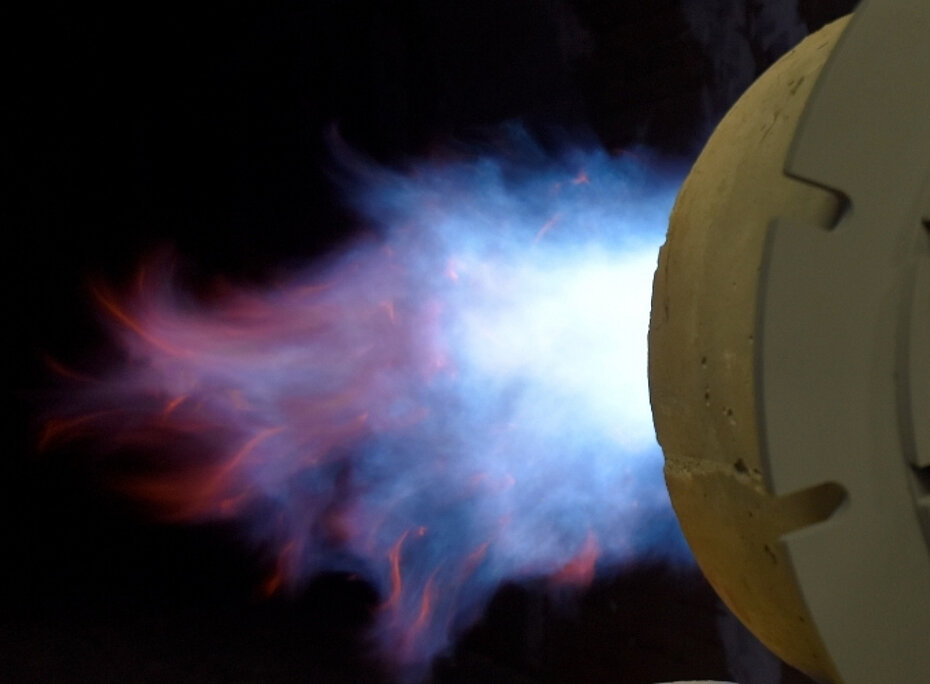
North American HiRAM®:
Large-capacity, low NOx
High velocity burners like the North American HiRAM® were developed by North American in the early 1980's and dramatically improved many industrial heating processes. The burner’s low NOx is achieved by drawing furnace gases into the flame, which has much the same effect as vitiated combustion air. The North American HiRAM produces low NOx emissions without the complexities of flue gas recirculation (FGR) or staged air combustion.
NOx levels are affected by furnace temperature, fuel type, combustion air temperature, burner firing rate, and other furnace factors. Emissions can be reduced further with the use of FGR. In applications requiring Ultra-low NOx emissions, the North American HiRAM® LNI system should be considered.
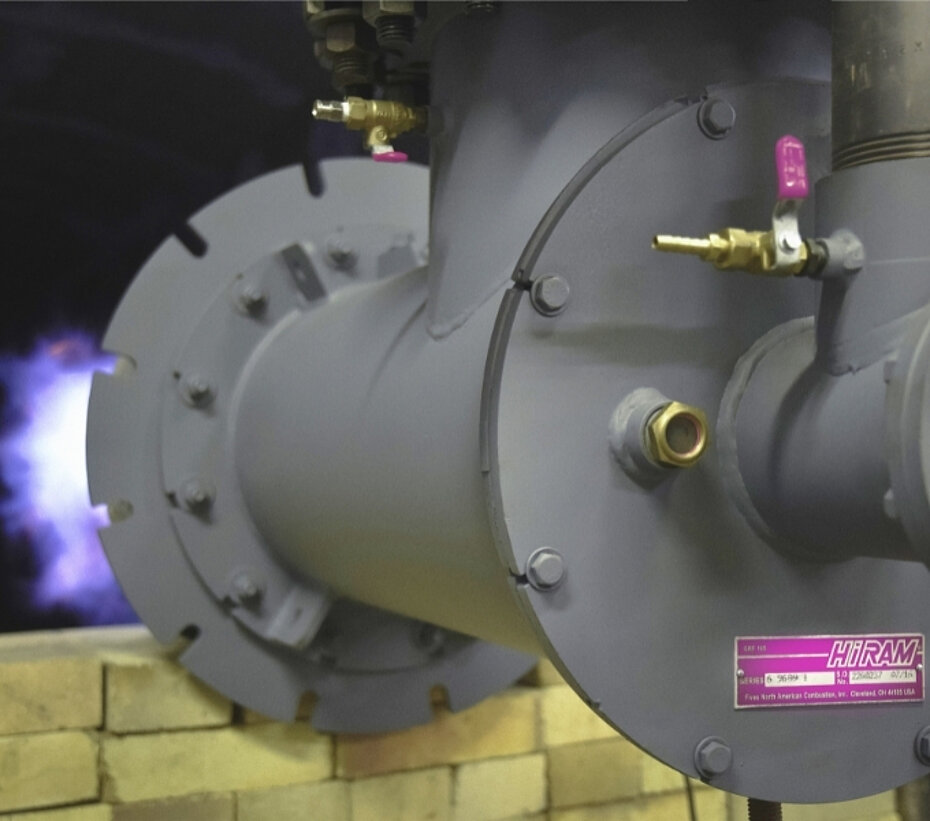
North American HiRAM® LNI: low NOx injection
The North American HiRAM® LNI burner technology takes advantage of the largest source of “free” FGR—the furnace itself—resulting in Ultra-low NOx emissions in high temperature applications.
This technology controls peak flame temperature and reduces in-flame oxygen concentration and residence time. LNI systems operate as a low-NOx, high-velocity burner when the furnace temperature is below 760°C (1,400°F). Above this temperature, fuel is switched from the center gas tube to strategically positioned nozzles adjacent to the burner tile port.
The fuel and air streams entrain large volumes of products of combustion. This greatly reduces the local oxygen concentration. In the flame envelope, these entrained gases limit maximum combustion temperatures and level out temperature spikes to reduce NOx emissions.
All combustion takes place within the furnace, providing short high-temperature residence times that inhibit NOx production. After combustion, the gases lose their heat through radiation and convective heat transfer to the work. These cooled gases travel throughout the furnace and are again entrained by the burner air and fuel jets, sustaining the NOx inhibiting process.