Building the cement plant of the future
Take a step toward sustainable cement production
The global cement industry is facing pressure to increase efficiency while adhering to ever stricter environmental regulations and CO2 reduction objectives. Our solutions are developed to address these challenges with the supply of the most modern installations for many different applications.
Preserving precious resources
- Electrical energy: our ground breaking FCB Horomill®, equipped with its aerodecantor and FCB TSV™ Classifier achieve the highest product quality with the lowest electrical consumption of the market either in raw meal, cement, slag or other materials grinding.
- Zero water: thanks to the use of FCB Horomill® for raw meal and cement grinding and Fives TGT® common process filter not only the grinding workshops can be water free but also the complete plant.
Limiting direct plant CO2 emissions
- Clinker substitute: our utmost flexible flash calcination circuit can turn the wider range of clays into artifical pozzolana with lower energy consumption.
- Clinker substitution: thanks to FCB Horomill® unique grinding technology, equipped with advanced control principles and high drying capacity gas circuit, we can produce cement with the lowest clinker content.
Drastically reducing the use of fossil fuels
Alternative fuels substitution: we developed several calciner systems to process up to 100% of alternative fuels replacing fossil fuels. According to their density, size, composition and moisture, our FCB Zero-NOx Preca hot spot calciner, FCB In-line Preca calciner and/or FCB Preca-Max® calciner will be the solution.
Leading the cement and concrete industry to the next level of circular economy
FCB Rhodax®, through differential crushing, transforms deconstruction concrete into a 100% recyclable resource. The liberation of its original components generate new aggregates, sand and cement paste. This paste can either be reintroduced in the burning line to produce low CO2 clinker or be used as a cement additive after recarbonation process, capturing CO2 from the kiln fumes.
Our commitment toward better industry
Fives is a key partner for cement manufacturers, helping them face the challenges posed by climate change and environmental regulations. We are deeply involved. Our process equipment, technologies and complete plant solutions offer the highest levels of energy efficiency, emissions control and product quality to reduce cement industry's CO2 footprint. Committed to institutions whose policy is the decarbonation of industry, we are proud to build today the plants of tomorrow.
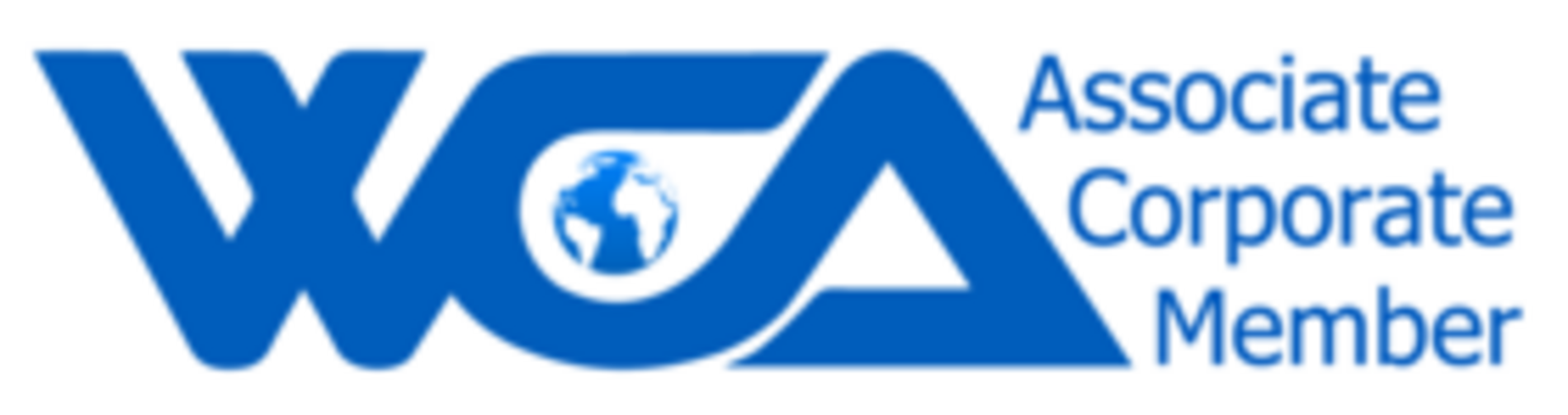
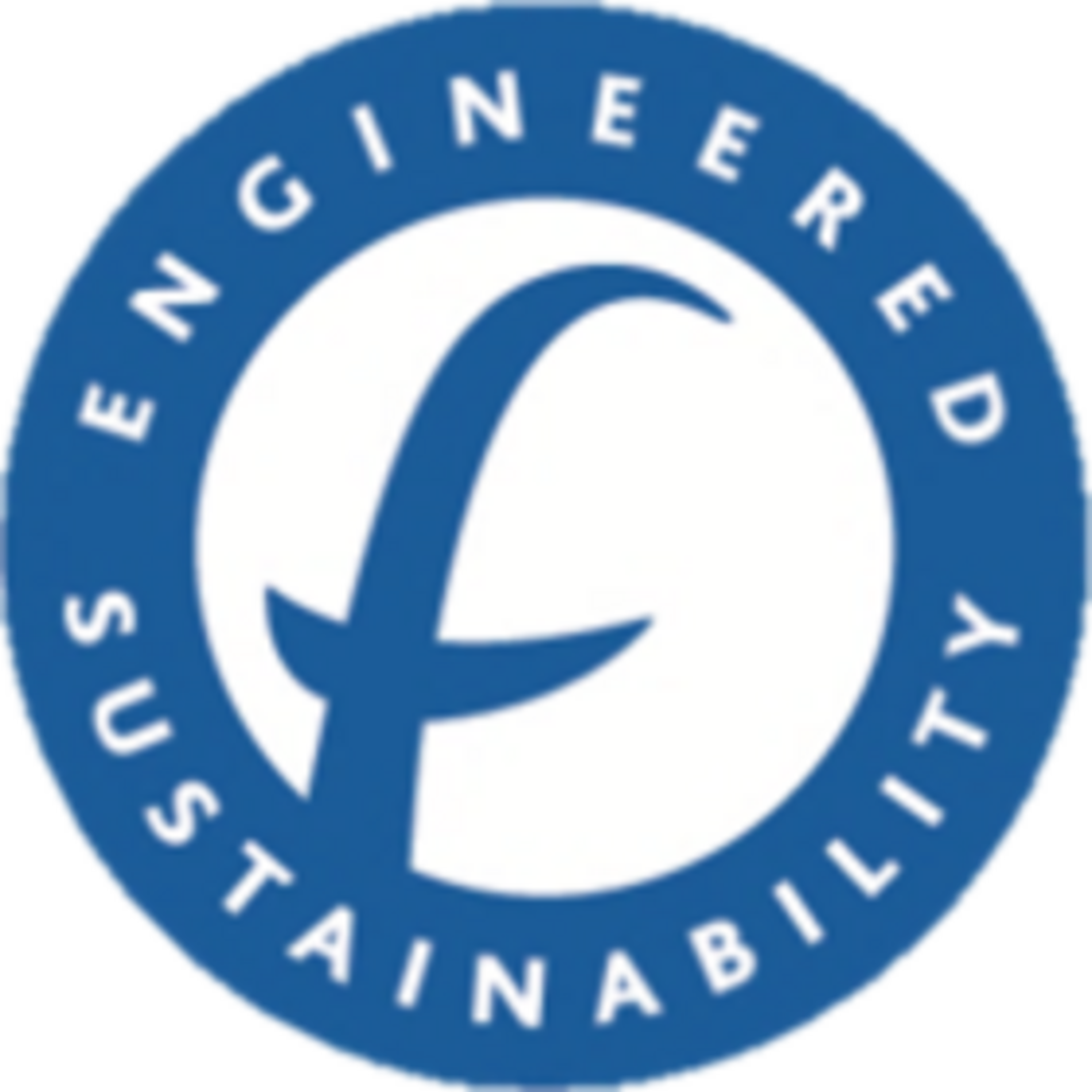
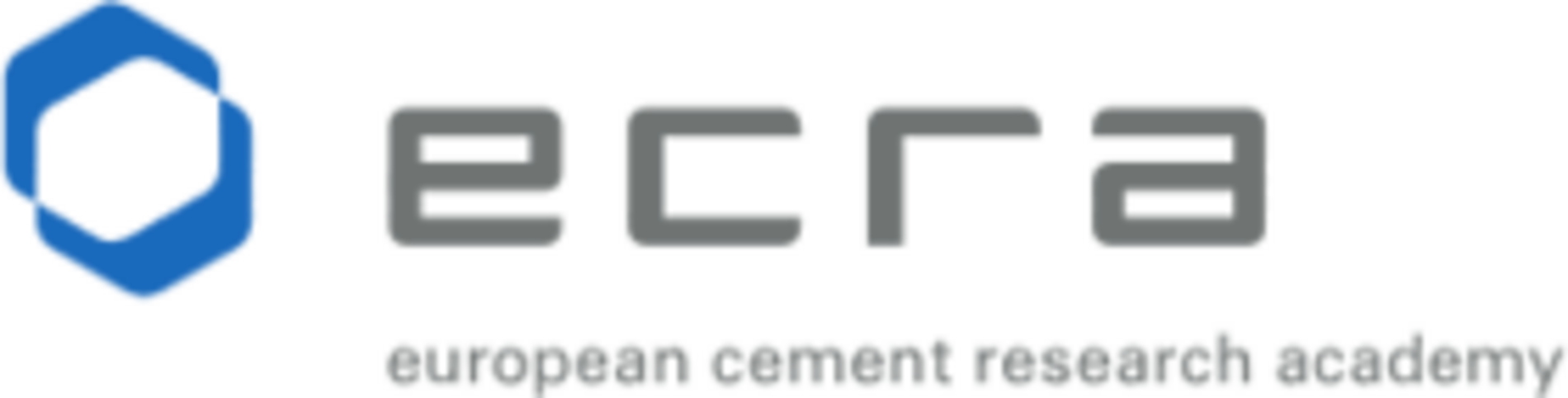
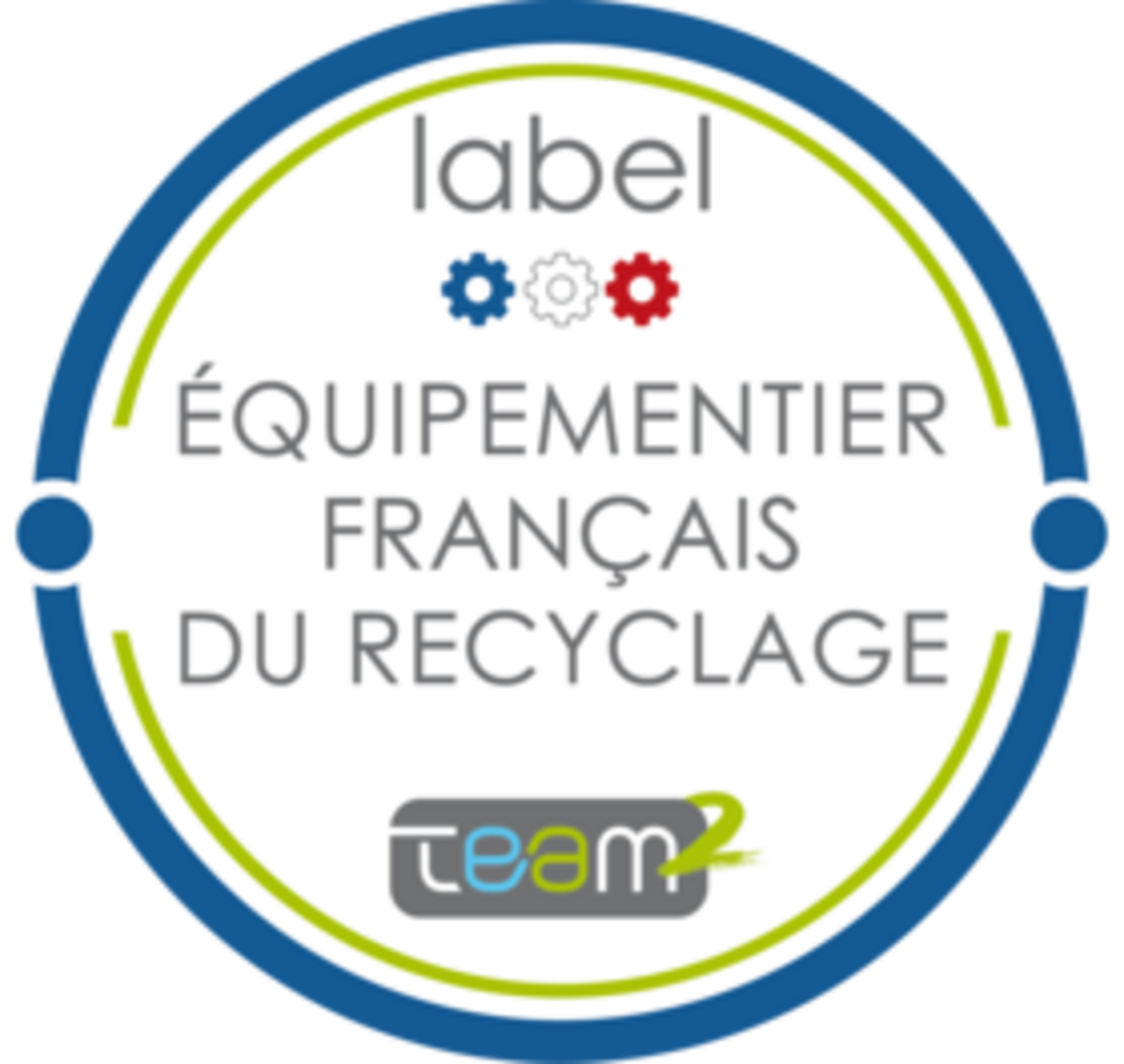