Clay calcination
FCB Flash calciner
Reducing the cement industry’s carbon footprint
Calcined clay is widely recognized as a sustainable substitute for cement clinker in the production of cementing materials. Reducing clinker use by 50% and replacing it thanks to calcined clay has no impact on the final concrete resistance, but offers a 40% reduction in CO2.
Fives’ FCB Flash Calciner is a comprehensive clay calcining solution that helps our clients meet both production and environmental goals. Committed to driving innovation for a more sustainable cement industry, we are proud to offer cost-effective and environmentally friendly equipment.
Flexible and reliable calcination of a wide range of materials
Our FCB Flash Calciner can be used with a wide range of clay materials. Its advanced technology prevents the raw materials from overheating. This is essential for producing highly amorphous pozzolan (an alternative cementing material) through calcination of kaolin or of clays containing kaolinite.
The equipment offers emissions reduction along with many other benefits:
- High flexibility due to fast warm-up
- Stable temperature control
- Accurate control of kaolinite dehydroxylation
- Highly activated clay
- Low energy consumption through heat recovery
- Variable capacity
- Outstanding end product with high consistency and low attrition
- Lower maintenance needs
- Compact footprint
- Low CAPEX for new plants
- Simplified management thanks to its state-of-the-art automation system
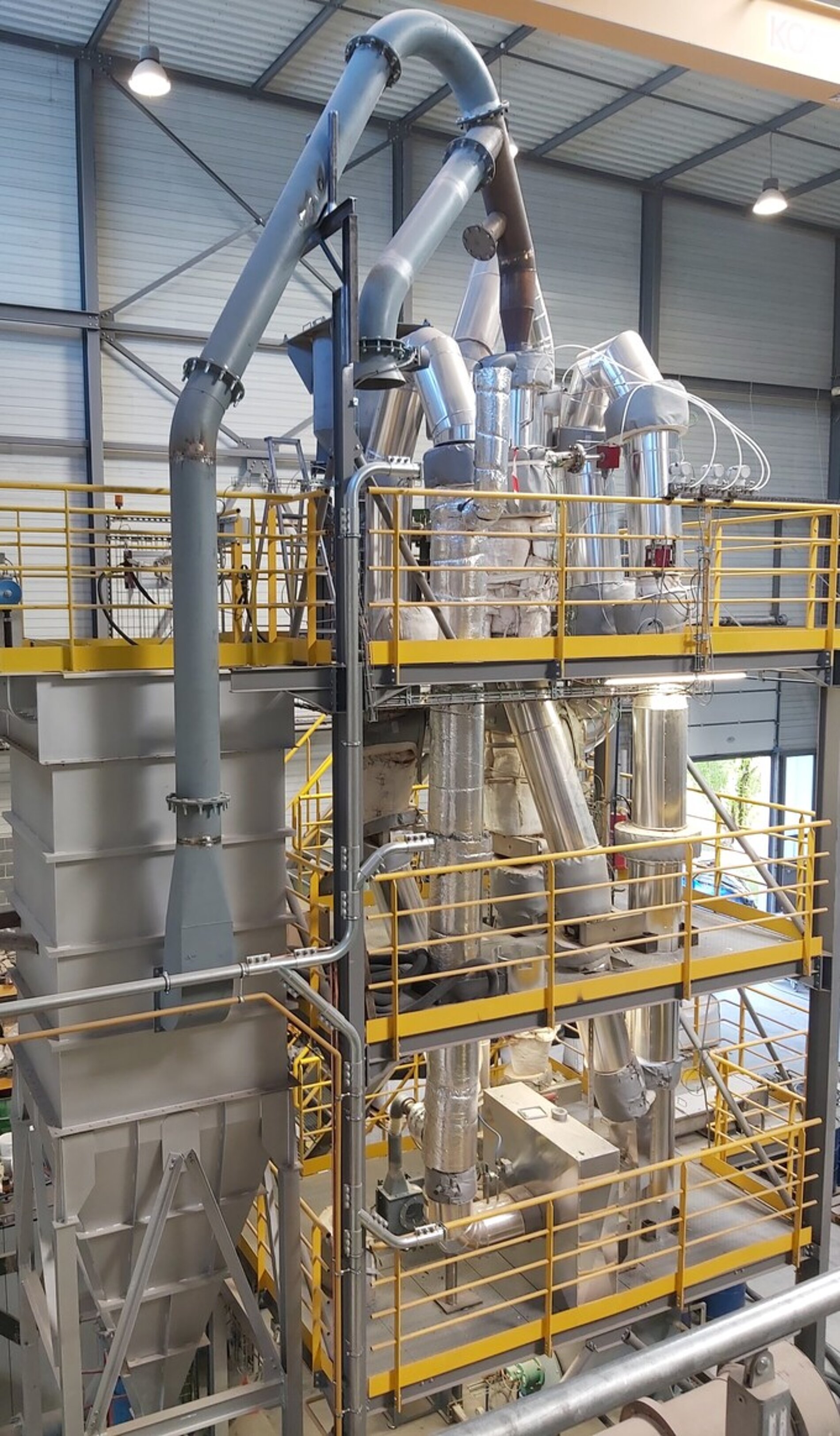
drying and grinding raw material
- Crushed material (<50 mm / <2 in) is ground with a dedicated mill and classifier for increased fineness (0-160 μm)
- Raw materials are dried using hot gases from the preheater outlet
- Once the dried material has achieved <1 % humidity, it is conveyed to the top of the preheater
PREHEATING AND CALCINING
- The FCB Cyclones provide a multistage preheating and one stage of calcining
- The FCB Flash Calciner is based on indirect firing providing an optimum temperature control and the possible use of alternative fuels and other energy sources
COLOR CONTROL
To avoid reddish color during calcination, iron oxides are reduced to the magnetite form by a reducing atmosphere maintained down to the stability temperature of the magnetite. Unlike conventional methods, our principle consists in dissociating the reduction phase from the calcination by performing it only during cooling, thus allowing:
- a wide range of alternative fuels use thanks to combustion with air excess
- reduced energy combustion as no afterburner is required
- limited use of reducing gases
COOLING
High-efficiency cyclones offer a two-stage cooling process, featuring:
- Low pressure drop
- Slope at inlet to avoid build-up
- Large cone outlet for smooth material flow
- Upper cyclones designed to boost efficiency
- Heat recovery
GAS TREATMENT
Our filtering systems allow for efficient pollutants neutralization and optimized reagent consumption during raw materials process:
- Dry scrubbing (lime injection) to reduce SOx emissions
- Regenerative Thermal Oxidizer system to treat VOC & HC
- Active coal injection to capture heavy metals and dioxins
- SNCR injection at HGG outlet for NOx reduction.
FIVES BY YOUR SIDE FROM FEASIBILITY STUDIES TO INDUSTRIAL PRODUCTION
From the early stage of your project, we carry out feasibility studies and materials characterization through an operational pilot plant, reliable predictive model of the future production tool.
The flexibility of our system lies in the choice of the flash process, enabling:
- to process a wide variety of clay mixtures
- to maximize the use of alternative fuels and other energy sources
- to optimize the calcining temperature thus significantly reduce the energy consumption of the production line, compared to a rotary kiln solution, while ensuring improved quality control.