AddUp launches a new generation of 3D metal printing machine: FormUp®350
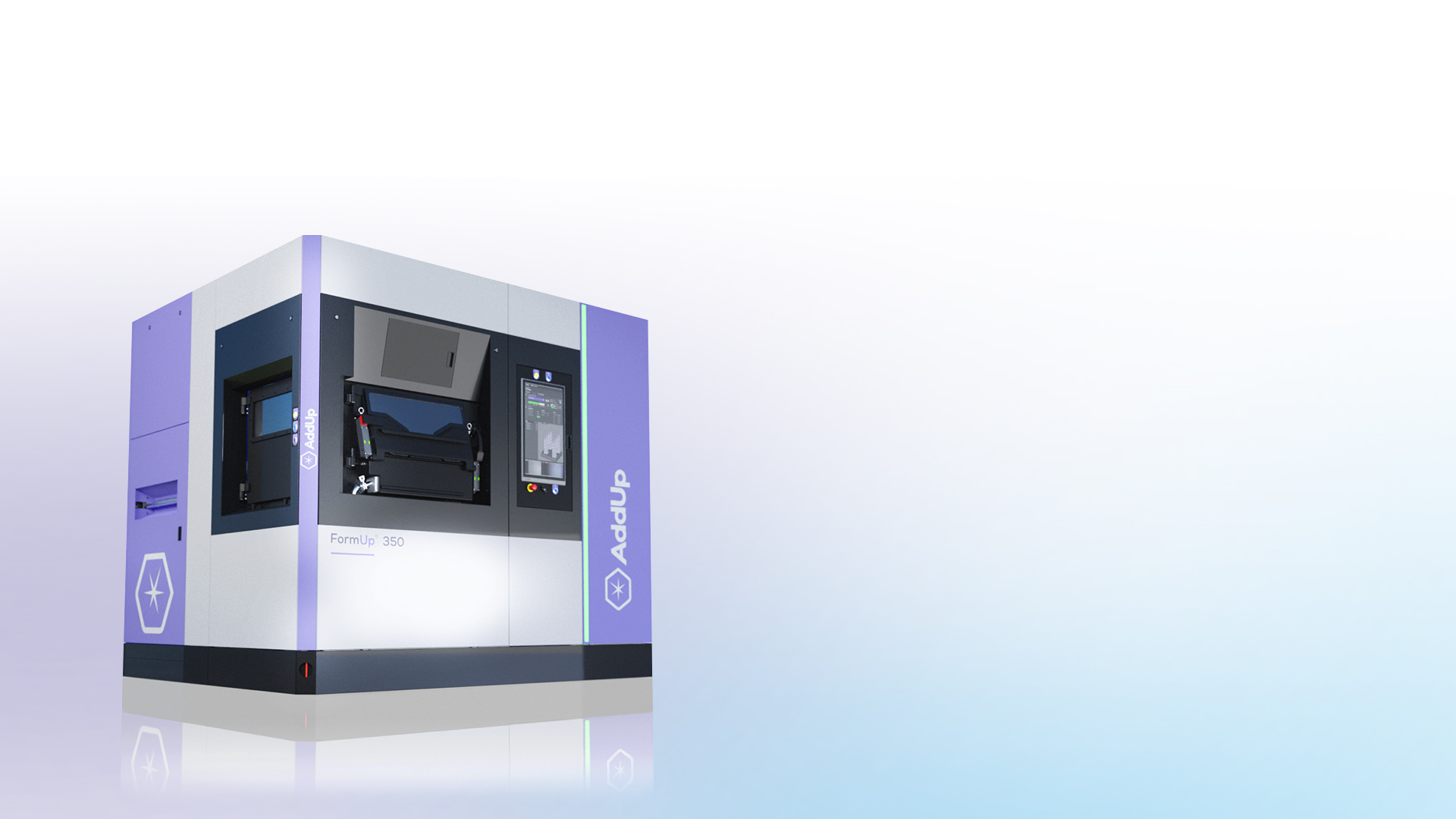
AddUp, a joint venture created by Michelin and Fives in 2016, has announced the introduction of its latest metal 3D printing machine using laser powder bed fusion (L-PBF) technology.
FormUp 350 allows to operate in complete safety, to produce perfectly reproducible series of parts at levels of productivity never achieved before,
by relying on a modular and scalable architecture. FormUp 350 delay the machine obsolescence and keep up a high level of performance
As a results of two years of advance research and test in AddUp’s workshop, FormUP 350 new generation is a solution designed for the industrial challenges such as : Safety, Productivity, Quality and obsolescence
Operate safely
The new generation of FormUp 350 can be used safely with all types of metal powders, reactive or not, with fine or medium granulometry. Operators will be able to work in complete safety using an innovative autonomous powder module developed exclusively with the AZO company, ensuring the storage, conveying, recovery and sieving of the powder, with all operations being carried out automatically in a closed circuit in an inert atmosphere. Exposure to fumes and smelting residues is controlled, using an automatic passivation filter system that ensures safe waste disposal. The passivation of soot and powders recovered during filtration is done by adding a calcium carbonate powder. This removes the risk of flammability from the waste and it can be processed safely.
Produce series of parts perfectly reproducible
The new generation of FormUp 350 allows us to meet all the quality requirements of our customers, covering all industrial fields from aeronautics, space or luxury, including motorsports, defense, medical. All the parameters of the machine are accessible according to the needs of the users from a simplified standard use to an expert mode use. Specific manufacturing recipes can be developed for each application, to find the best balance between productivity and quality for each part. AddUp provides support to our customers with a unique application service on the market, based on the expertise developed in our parts manufacturing activity. AddUp benefit from 40 printing machines installed in Europe to date, as well as a strong experience in post-processing and finishing of parts (heat treatment, machining, etc.), allowing us to supply our customers with finished parts that are ready for use.
The lasers with a geometric precision of the spot center of each laser at 35 µm, are all equipped with a "3-axis" optical chain, a high-end technology that guarantees both positioning accuracy (24-bit resolution) and laser beam quality. This accuracy is key for multi-laser applications on a single part.
The AddUp NCore software embedded in the machine is capable of processing large production files of more than 80 GB in one go, enabling complex parts to be produced. AddUp Dashboards, a software solution for traceability and analysis of all production data, allows the tracking of 80 manufacturing parameters and the automatic editing of production conformity reports. In terms of monitoring, we have developed a system for monitoring the quality of the fusion, continuously measuring the power emitted by the laser and the temperature of the fusion, and real-time analysis technology of the powder spreading quality, which checks the absence of defects on the surface of the powder bed in less than a second and triggers a second run of the coating system if necessary. The FormUp 350 is the only machine on the market with an interchangeable coating device. Our customers can choose the powder spreading system that best suits their needs: a scraper system or a roller system. The latter provides better repeatability for certain medium powder applications. It also allows the use of fine powders, for unsupported manufacturing of cantilevered parts and improved surface finishes. A heating plate up to 200°C reduces stress concentrations and the risk of part deformation.
Produce series of parts at productivity levels never achieved before
The new generation of FormUp 350 can produce using four 500 W lasers simultaneously, each laser covering the entire surface of the tray. The bidirectional coating system reduces non-productive times by 40% faster powder spreading cycles than monodirectional spreading. The powder supply is done in masked time, using the autonomous powder module mentioned above.
AddUp's teams have also developed innovative solutions to maximize the machine's uptime:
- A long-life fume treatment module (filter replacement interval greater than one year)
- The use of the Cross Jet technology limits any soiling of the laser protection glass during manufacturing.
- Optimized sealing of the production chamber to reduce inerting times. 15 minutes are sufficient to reach an oxygen level of 500 ppm.
- A cooling system for the machine’s Z-axis lowering the temperature of the platform at the end of production, allowing parts to be unloaded more quickly (2 hours to cool down from 200 to 65°C).
- A system of referencing platforms by probes allowing in a few seconds to adjust the positioning of the manufacturing trays and to check their flatness.
- A speed of calculation of trajectories unique on the market, up to 1000 times faster than real production. Thus 1.27 million trajectories are generated per second using the AddUp Manager software
Delay obsolescence with a modular and scalable machine
The modular design of the FormUp 350 machines allows our customers to configure and upgrade the machine according to their needs and to benefit from the latest technologies at any time, without replacing the machine.
We offer four configurations:
- STARTER, which brings together the essentials for research and development activities, designed for the use of non-reactive powders of medium grain sizes.
- EFFICIENCY, perfect to get started in additive manufacturing with confidence, with a wide range of powders (fine or medium, reactive or non-reactive).
- PRODUCTIVITY, the perfect answer for a high level of productivity and a high level of industrialization, with four lasers and an autonomous powder module.
- ADVANCED, designed for "expert" users who are looking to achieve the highest levels of productivity, quality and monitoring of the manufacturing process.
These configurations can be fully integrated into existing customer environments. It is possible to add new modules, options or equipment to delay the obsolescence of the first-generation machines.